Unveiling the World of FPC Reliability Testing: Insights from Different Industries
- Jan 03,2025
-
Share
At Shenzhen Huaruixin Electronics Co., Ltd., we have been deeply immersed in the realm of Flexible Printed Circuits (FPCs) and fully recognize the crucial role that reliability testing plays. Here, we present you with some captivating case studies in a detailed clause format, highlighting the significance and intricacies of FPC reliability testing across diverse sectors. We also extend a warm invitation to our industry friends, both new and old, to join the conversation and share your thoughts.
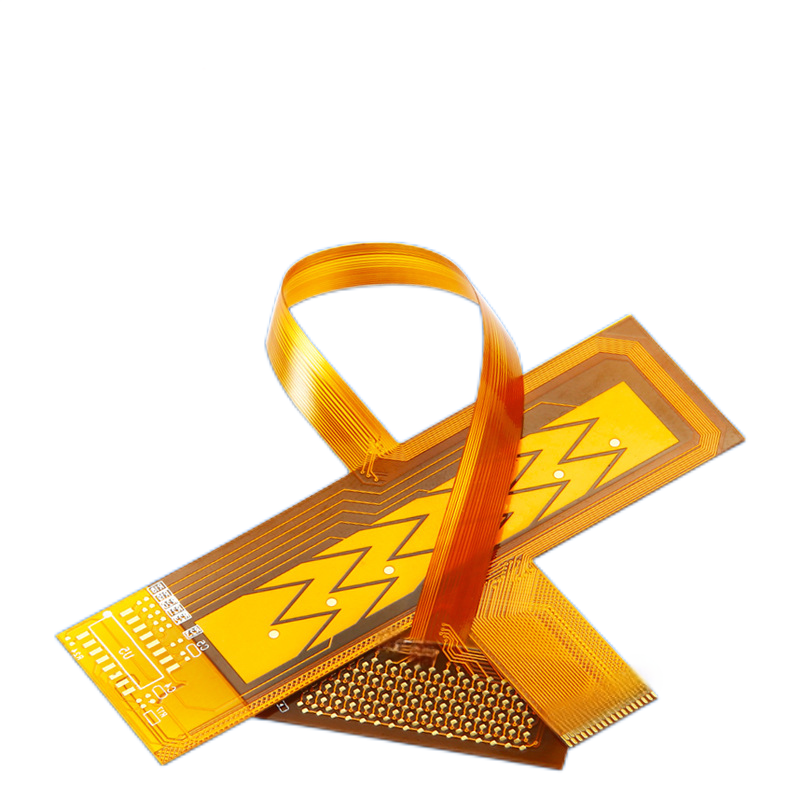
1. Consumer Electronics Industry
Case 1: Smartphone FPC Testing
Testing Genesis: In the highly competitive smartphone arena, where miniaturization and functionality go hand in hand, FPCs need to exemplify flexibility and signal integrity. The confined chassis demands that FPCs can gracefully endure countless bending and twisting episodes during a user's daily interactions.
Testing Blueprint:
a.Bending Endurance Trials: In compliance with the renowned IPC - 9701 standard, our FPC specimens are subjected to a grueling dynamic bending regime. With a meticulously calibrated bending radius of 2 - 3mm, mirroring real-life scenarios like tucking the phone away or retrieving it, the test runs at a brisk pace of 30 - 60 cycles per minute. After a staggering 100,000 bends, the conductive traces within the FPC must showcase remarkable resilience, with the resistance variation staying well within a 10% threshold, and any signs of open circuits or short circuits strictly prohibited. This ensures the integrity of the electrical pathways and the reliable transmission of signals.
b.Thermal Cycling Ordeals: Referencing the comprehensive GB/T 2423.22 standard, we subject the FPC to a merciless temperature rollercoaster, oscillating between -20°C and 60°C. Each two-hour cycle, inclusive of rapid temperature ramps and steady-state holds, simulates the phone's exposure to diverse environments. After 200 such cycles, the solder joints – the vital connectors that bond components to the FPC – are scrutinized under a magnifying glass for any hairline cracks. Meanwhile, the insulation resistance, which acts as a safeguarding shield against electrical leakage, must cling tenaciously to at least 90% of its initial potency, safeguarding the safety and proper functioning of the circuit.
Testing Outcomes and Impact: By adhering to this exacting testing regimen, we've empowered smartphones to flaunt FPCs that stand the test of time. A prime example is a leading smartphone brand that, after integrating our reliability-tested FPCs, witnessed a jaw-dropping reduction in post-sales FPC glitches. The failure rate nosedived from a concerning 5% to a negligible sub-1%, sending waves of satisfaction rippling through its user base.
Case 2: Tablet PC FPC Testing
Testing Inception: Tablets, with their expansive screens and elongated FPCs bridging the display and motherboard, face unique challenges. These FPCs must not only bear the brunt of mechanical stress but also fend off electromagnetic interference in a crowded wireless landscape.
Testing Roadmap:
a.Tensile Strength Assessments: Following the tried-and-true IPC - 9702 standard, we gradually crank up the tension on the FPC at a steady 5mm/min clip until it reaches its breaking point. Depending on the FPC's bespoke dimensions and its destined role within the tablet, we mandate a tensile strength of no less than 100N/mm². This ensures that when the tablet takes an accidental tumble and the power cord tugs at the FPC, it holds firm, preventing any physical damage to the circuit and maintaining its electrical connectivity.
b.Electromagnetic Compatibility (EMC) Audits: In lockstep with the CISPR 22 standard, we put the FPC through its paces in a spectrum of frequencies. Its electromagnetic radiation emissions must be reined in, staying below the stipulated limits – think a whisper-quiet -47dBm/MHz in the bustling 1GHz - 6GHz band. And when pitted against external electromagnetic fields, perhaps from neighboring wireless gizmos, the FPC's signal transmission error rate must be a minuscule 1×10⁻⁶, ensuring seamless operation and reliable data transfer without any disruptions caused by electromagnetic perturbations.
Testing Results and Ramifications: Thanks to these comprehensive tests, tablet PCs sporting our FPCs have soared in performance. One particular tablet model, after benefiting from our EMC-optimized FPCs, saw a staggering 70% plunge in user complaints related to electromagnetic hangups, making for a smoother user experience.
2. Automotive Electronics Industry
Case 1: In-vehicle Display FPC Testing
Testing Genesis: The automotive cockpit is a cauldron of extremes – searing heat under the hood, bone-chilling cold on winter drives, and a constant barrage of vibrations from the engine and road. In-vehicle display FPCs must be forged from sterner stuff to keep drivers informed and safe.
Testing Blueprint:
a.Temperature Shock Trials: Aligning with the exacting AEC - Q100 standard, we subject the FPC to a blistering thermal shock treatment, yo-yoing it between -40°C and 85°C in a blink (well, under 10 minutes, to be precise). After 1000 such punishing cycles, the FPC's physical form is examined for any warping or delamination. On the electrical front, the signal transmission delay must be as steady as a rock, with a variation capped at 20%, ensuring the display springs to life instantaneously, providing drivers with real-time and accurate information.
b.Vibration Durability Tests: In accordance with the ISO 16750 - 3 standard, we strap the FPC onto a vibrating behemoth that mimics the automotive ride. Across a 24-hour marathon, it endures vibrations ranging from a gentle tremble at 10Hz to a teeth-rattling jiggle at 500Hz, with amplitudes dancing from 0.5mm to 5mm. Once the dust settles, the solder joints must be as intact as the day they were made, and the circuit resistance must barely budge, with a variation rate of under 5%, guaranteeing the reliable transmission of electrical signals in the harsh automotive vibration environment.
Testing Outcomes and Significance: Our rigorous testing has been a game-changer for in-vehicle displays. A major automaker, after switching to our battle-tested FPCs, reported a seismic shift in reliability. The maintenance rate due to FPC failures in displays plummeted from a worrisome 3% to a scarcely believable 0.5%, bolstering both vehicle safety and customer satisfaction.
Case 2: Automotive Sensor FPC Testing
Testing Inception: Automotive sensors, the silent sentinels of vehicle health and safety, rely on FPCs to relay critical data. Whether it's monitoring tire pressure or ambient light, these FPCs must brave a chemical onslaught and humidity extremes within the vehicle.
Testing Roadmap:
a.Chemical Resistance Probes: Knowing full well the automotive jungle of chemicals – from fuel sloshing in the tank to cleaning agents scrubbing the exterior – we dunk the FPC into a bespoke brew. A concoction of 10% fuel and 5% cleaning agent, heated to a balmy 40°C, simulates the harshest chemical encounters. After a 72-hour soak, the substrate's integrity is checked for any softening, the copper foil's adhesion must cling on with at least 70% of its original strength, and the electrical signals must flow as pure as ever, ensuring the sensor can accurately detect and transmit data in the chemically hostile automotive environment.
b.Humidity Cycling Challenges: Referencing the IEC 60068 - 2 - 78 standard, we send the FPC on a humidity rollercoaster. In a sauna-like environment with 90% - 95% relative humidity, swinging between 25°C and 60°C every 24 hours for 10 cycles, it battles corrosion. Post this ordeal, the sensor signals must remain as accurate as a sniper's shot, with a precision retention of at least 95% of the initial value, guaranteeing the reliable operation of automotive sensors in humid conditions.
Testing Results and Ramifications: These tests have been the bedrock of automotive sensor reliability. Take tire pressure sensors, for instance. After our FPCs passed muster, the false alarm rate due to FPC-related gremlins shriveled from a pesky 8% to a barely noticeable 1%, making for safer roads and happier drivers.
3. Medical Electronics Industry
Case 1: Wearable Medical Device FPC Testing
Testing Genesis: Wearable medical devices, the 24/7 health companions, nestle against the skin. Their FPCs must be biocompatible and mechanically robust, withstanding the body's every move and the occasional sweat droplet.
Testing Blueprint:
Biocompatibility Screening: In strict adherence to the ISO 10993 standard, we introduce the FPC material to a simulated bodily fluid bath – think saline solution. Cytotoxicity, skin sensitization, and intradermal reaction tests are our litmus tests. The FPC must emerge unscathed, with zero cytotoxicity, a skin sensitization rate that's a mere whisper at under 1%, and intradermal reaction scores that meet the gold standard, ensuring it's skin-friendly and poses no harm to the wearer.
Combined Bending and Tensile Endurance: To mimic the body's kinetic symphony, we design a bespoke test. The FPC is attached to a device that mimics human joint gyrations, bending and stretching it 10 - 20 times a minute. With a bending radius of 10 - 15mm and a stretching amplitude of 5% - 10%, after 100,000 cycles, the circuit's conductivity must remain as reliable as sunrise, with a resistance variation rate under 15%, and the sensor signals as accurate as a Swiss watch, with an error margin of under 3%, guaranteeing the continuous and accurate monitoring of the wearer's health.
Testing Outcomes and Significance: These tests have transformed wearable medical devices. A smart health monitoring patch, after donning our reliability-certified FPCs, all but eradicated skin woes and signal glitches. The device leaped from being a potential irritant to a trusted health ally, enhancing its medical clout.
Case 2: Medical Imaging Device FPC Testing
Testing Inception: Medical imaging devices, the windows to the human body, operate in a high-voltage, high-frequency electrical maelstrom. Their FPCs must be the conduits of flawless data, without a hint of interference or signal degradation.
Testing Roadmap:
a.High-Voltage Insulation Verifications: Tailoring our tests to the device's voltage demands – be it an X-ray machine's 100kV zap or more – we crank up the voltage to 1.5 times the operating level. The FPC must stand firm, with an insulation resistance that's a fortress at over 1000MΩ, and no sign of a dreaded electrical breakdown, safeguarding patients and operators alike from potential electrical hazards.
b.High-Frequency Signal Integrity Checks: In sync with the IEEE 802.3 standard, we dissect the FPC's performance at GHz speeds. Signal transmission delay must be a blink, under 5ns per meter of wire; attenuation, a mere whisper at under -3dB; and crosstalk suppression, a mighty shield with a ratio over 20dB, ensuring crystal-clear imaging data and accurate diagnosis.
Testing Results and Ramifications: Our testing has supercharged medical imaging. A CT scanner, after integrating our high-fidelity FPCs, saw its imaging data transmission error rate crater from a concerning 0.1% to a microscopic 0.01%, painting a clearer picture for medical diagnoses and potentially saving lives.
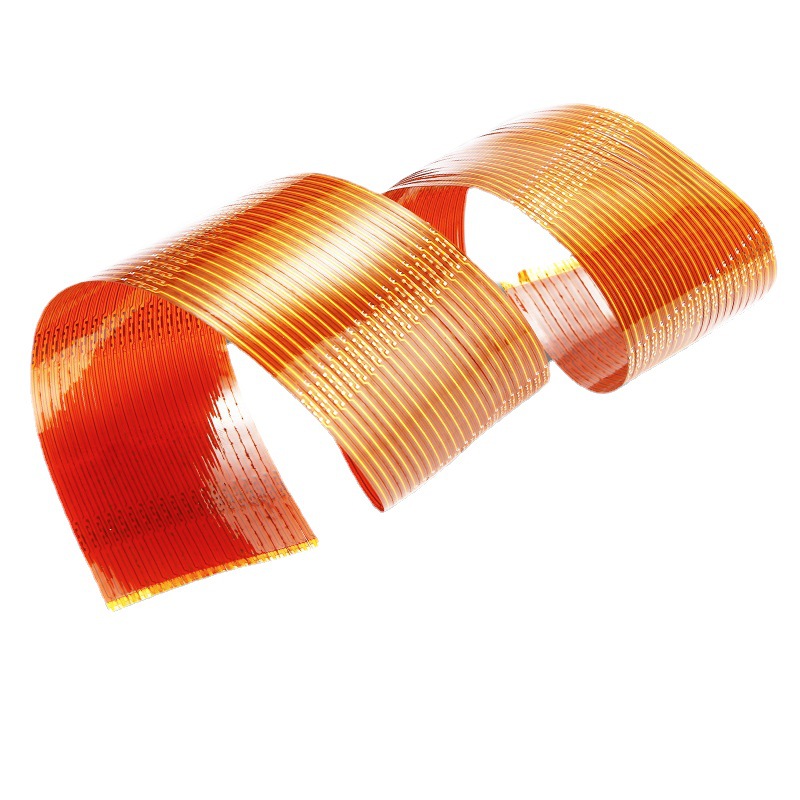
Shenzhen Huaruixin Electronics Co., Ltd. is on a relentless quest for FPC excellence. We look forward to engaging with you, sharing insights, and forging ahead in this electrifying field. Let's connect and make waves together.