In the realm of Flexible Printed Circuit (FPC) manufacturing, guaranteeing the performance and reliability of FPCs is of paramount significance. A critical determinant in this regard is the judicious selection of the flexible substrate, which demands a comprehensive consideration from multiple aspects and across various practical application domains.
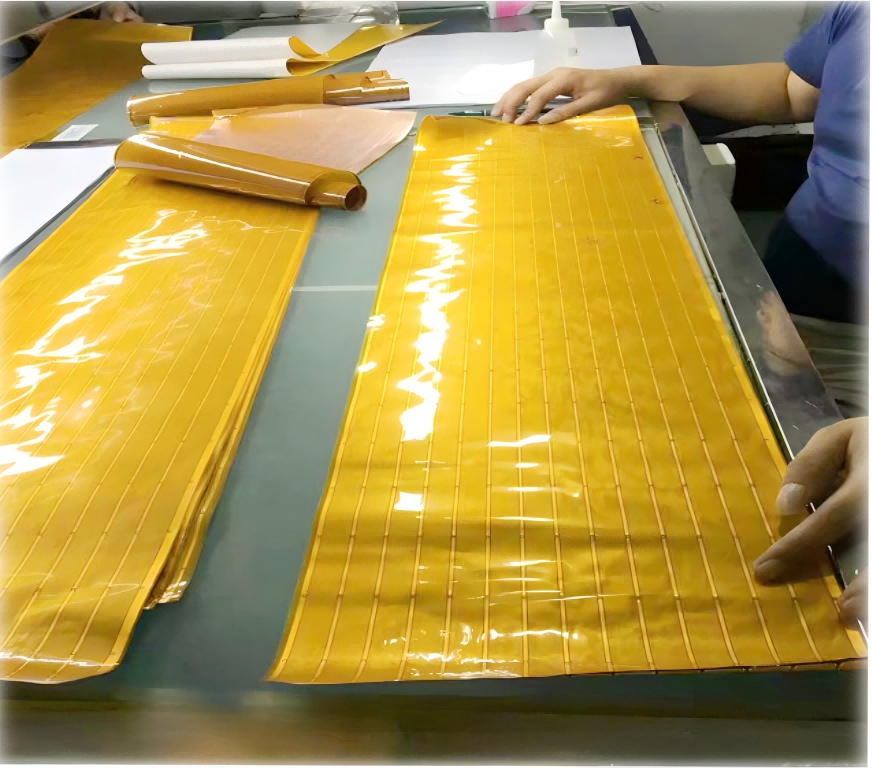
In the consumer electronics industry, exemplified by smartphones, tablets, smartwatches, and wireless earbuds, polyimide (PI) or polyester (PET) films are prevalently employed as substrates. PI, renowned for its outstanding flexibility, thermal endurance, and electrical conductivity, is well-suited to the dynamic and often compact environments of these devices. In a smartphone's intricate circuitry, where FPCs serve as the conduits for interconnecting components such as high-resolution displays, miniature cameras, and power-efficient batteries, the PI substrate's mechanical resilience and stable electrical properties ensure seamless signal transmission and reliable operation, even under the duress of repeated mechanical stress and temperature excursions.
The automotive electronics sector presents a more challenging milieu. Consider an automotive engine control unit (ECU) or an advanced driver-assistance system (ADAS). Here, the FPCs are subjected to extreme temperatures, persistent vibrations, and potential exposure to corrosive automotive fluids. High-performance polyimide films emerge as the substrate of choice due to their remarkable thermal stability, vibration damping capabilities, and chemical inertness. These properties enable the FPCs to maintain signal integrity and mechanical robustness, thereby safeguarding the critical functions of the vehicle's electronic subsystems and contributing to overall driving safety and performance.
Medical electronics is another domain with stringent requirements. Implantable medical devices like cardiac pacemakers, implantable cardioverter-defibrillators (ICDs), and neural prosthetics necessitate substrates that not only possess excellent electrical insulation and mechanical durability but also exhibit biocompatibility and bio-stability. Specialized medical-grade polymers, which have undergone rigorous biocompatibility testing and comply with regulatory standards, are meticulously selected. These substrates ensure that the FPCs can function reliably within the human body's physiological environment, without eliciting adverse immunological responses or compromising the long-term viability of the implanted device.
In the aerospace and avionics industries, FPCs are deployed in aircraft cockpit instrumentation, flight control systems, and satellite communication modules. The substrates must endure the rigors of high-altitude conditions, including extreme temperature differentials, intense radiation, and mechanical stress during takeoff, flight, and landing. Polyimide-based substrates with enhanced radiation resistance and thermal cycling capabilities are favored. Their ability to maintain dimensional stability and electrical performance under such harsh conditions is vital for the reliable operation of critical aerospace systems and the safety of air travel.
For industrial automation and robotics applications, such as robotic arms in manufacturing plants or sensor arrays in industrial control systems, the FPCs need to withstand continuous mechanical motion, potential exposure to industrial chemicals, and a wide range of operating temperatures. Polyimide substrates with high tensile strength and chemical resistance are commonly utilized. They enable the FPCs to provide stable electrical connections between sensors, actuators, and control units, ensuring the precision and reliability of industrial processes and robotic operations.
In conclusion, the selection of the flexible substrate for FPCs is a highly nuanced and application-specific process. It demands a profound understanding of the unique demands and constraints of each industry. At Shenzhen Huaruixin Electronics Co., Ltd., leveraging our extensive experience and technical expertise in FPC production and sales, we are dedicated to collaborating with our clients. We welcome both new and established customers to engage in in-depth discussions and knowledge-sharing initiatives, with the shared objective of optimizing substrate selection and thereby enhancing the performance and reliability of FPCs in a multitude of applications.