Methods to Reduce the Failure Rate of FPCs in Vehicle Environments
- Dec 20,2024
-
Share
Base Material: The choice of the base material is fundamental. Polyimide (PI), a staple in the FPC realm, is a preferred material for FPCs in automotive applications due to its excellent heat resistance, chemical stability, and mechanical flexibility. High - quality PI with a suitable thickness can withstand the extreme temperature variations in a vehicle, which can range from - 40°C in cold starts to over + 85°C in hot parked conditions. For example, a PI substrate with a thickness of 25 - 50 microns can provide a good balance between flexibility and durability. This substrate serves as the reliable foundation for the complex circuitry and component attachments within the FPC assembly.
Conductor Material: Copper, the quintessential conductor in FPCs, is used in automotive applications. However, for automotive applications, it's crucial to use high - purity copper with good conductivity and resistance to oxidation. The thickness of the copper foil also matters. Thicker copper foils, such as 35 - 70 microns, can handle higher currents and are less prone to breakage during bending or vibrations. Additionally, the use of plated copper with a suitable finish, like gold - plating in connector areas, can enhance conductivity and corrosion resistance. The copper traces, with their precisely defined widths and pitches, are the pathways for the efficient transmission of electrical signals throughout the FPC.
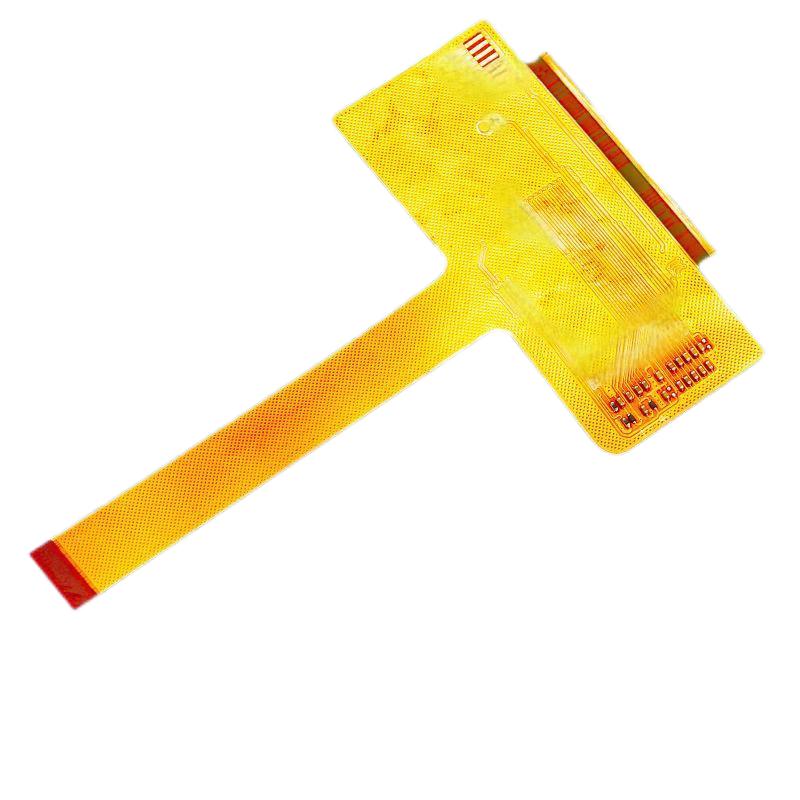
Bend Radius and Flexibility: In a vehicle, FPCs often need to be routed through tight spaces and bent to fit around various components. Designing with an adequate bend radius is essential to prevent conductor cracking and layer delamination. A general rule is to maintain a minimum bend radius of at least 5 times the thickness of the FPC. For instance, if the FPC is 0.2mm thick, the minimum bend radius should be 1mm. Using flexible coverlays and incorporating stepped or curved designs in areas that require sharp turns can further enhance the FPC's flexibility and reduce the risk of damage due to repeated bending. The coverlay, typically a thin layer of insulating material, protects the circuitry while allowing for the necessary flexibility.
Stiffener Integration: To enhance the FPC's resistance to vibrations and mechanical stresses, stiffeners can be integrated at critical points, such as connector areas. These stiffeners are usually made of a rigid yet lightweight material like FR - 4 (Flame - Retardant 4). They provide additional support to the FPC without sacrificing its overall flexibility. The size and location of the stiffeners are determined through finite - element analysis and mechanical simulations to ensure that they effectively reduce stress concentrations and prevent damage. The stiffeners act as a mechanical reinforcement, safeguarding the integrity of the FPC's delicate circuitry and connections.
Impedance Control: Maintaining proper impedance is crucial for signal integrity, especially for high - speed signals in automotive infotainment systems and other electronics. The impedance of FPC traces is carefully designed and controlled. For example, for LVDS (Low - Voltage Differential Signaling) signals, the impedance is typically designed to be around 100 ohms. Precise control of trace width, spacing, and the dielectric constant of the substrate material is necessary to achieve the desired impedance and reduce signal reflections and degradation. The impedance matching is a meticulous process that requires advanced design software and engineering expertise to ensure optimal signal transmission.
EMC Measures: The automotive environment is filled with various electromagnetic sources that can cause interference. To reduce electromagnetic interference (EMI) and ensure electromagnetic compatibility (EMC), several techniques can be employed. The use of ground planes and shielding layers in the FPC design is effective. For example, a ground plane adjacent to the signal layers can act as a shield against external EMI. Additionally, ferrite beads or EMI filters can be added to the FPC to suppress high - frequency noise and prevent it from affecting the performance of the connected components. These EMC components and design strategies are essential to maintain the reliable operation of the automotive electronics systems that rely on the FPCs.
Precision Manufacturing Equipment: The use of high - precision manufacturing equipment is essential to produce FPCs with consistent quality. Advanced printing, etching, and lamination machines are used to ensure accurate circuit pattern transfer, proper etching of unwanted copper, and reliable layer lamination. For example, photolithography machines with a high resolution of up to 25 microns can accurately define the fine traces on the FPC. The etching process, which involves the use of specific etchant chemistries and carefully controlled parameters, removes the excess copper to create the desired circuitry.
Quality Control Processes: Comprehensive quality control processes are implemented to detect and correct any manufacturing defects. Visual inspection using high - magnification microscopes is carried out to identify surface defects such as scratches, dents, or delamination. Electrical testing includes continuity testing to ensure proper signal paths, insulation resistance testing to check for any short - circuits, and impedance measurement to verify the correct electrical characteristics. For example, in a batch of FPCs, any unit that fails the quality control tests is either repaired or rejected to prevent faulty products from reaching the market. The quality control procedures are in line with industry standards and are continuously refined to meet the evolving demands of automotive applications.
Temperature Cycling Tests: FPCs are subjected to temperature cycling tests to simulate the extreme temperature conditions in a vehicle. The FPCs are placed in environmental chambers and cycled through a range of temperatures from - 40°C to + 85°C for a specified number of cycles, typically several hundred to a few thousand cycles. This testing helps to identify any potential issues such as delamination, cracking, or changes in electrical properties due to thermal expansion and contraction. The temperature cycling exposes the FPCs to the harsh thermal stresses they may encounter during the vehicle's operation and lifetime.
Vibration and Shock Tests: Vehicles are constantly subjected to vibrations and shocks during operation. FPCs are tested under vibration and shock conditions to ensure their mechanical integrity. Vibration tests are carried out using shakers that can simulate the frequency and amplitude of vibrations experienced in a vehicle. Shock tests involve subjecting the FPCs to sudden impacts to check for any damage to the components or connections. These tests mimic the real - world mechanical forces that the FPCs must endure in the automotive environment and help to validate their durability and reliability.
By implementing these methods, the failure rate of FPCs in the challenging automotive environment can be significantly reduced, ensuring reliable performance and longevity of the components. Shenzhen Huaruixin Electronics Co., Ltd., with its extensive experience in FPC manufacturing, follows these best practices to provide high - quality FPCs for automotive applications.