In the domain of home appliance manufacturing, the judicious selection of materials for Flexible Printed Circuits (FPCs) is of utmost significance. The performance, durability, and safety of home appliances hinge substantially on the materials incorporated into their FPCs. Shenzhen Huaruixin Electronics Co., Ltd., leveraging its extensive experience in FPC production and sales, proffers invaluable insights and recommendations in this regard.

I. High-Temperature Resistance
Problems:
Numerous home appliances, such as ovens, hair dryers, and specific components within washing machines and air conditioners, generate copious amounts of heat during operation. In the absence of adequate high-temperature resistance in the FPC material, it may succumb to deformation, degradation of electrical properties, or even outright failure. For instance, the softening or melting of the substrate material could precipitate short circuits or open circuits, thereby jeopardizing the safety and functionality of the appliance.
Avoidance and Suggestions:
Selecting Appropriate Substrate Materials: Polyimide (PI) is a ubiquitously employed substrate material renowned for its exceptional high-temperature resistance. It can sustain its mechanical and electrical properties across a broad temperature spectrum. For applications entailing extremely elevated temperatures, such as in industrial-grade heating appliances, materials with enhanced heat resistance ratings or modified PI formulations can be contemplated. Additionally, advanced high-temperature polymers like liquid crystal polymers (LCPs) could also be evaluated, which exhibit remarkable thermal stability and are suitable for high-temperature FPC applications.
Thermal Management Design: Integrate heat dissipation features into the FPC design. This could entail the utilization of metal layers or heat sinks in strategic positions to conduct heat away from the critical regions of the FPC. Employing thermal vias and heat spreaders can optimize the heat transfer path. Moreover, designing proper ventilation or heat dissipation channels within the appliance chassis can mitigate the overall temperature exposure of the FPC. Implementing thermal simulations during the design phase can assist in predicting and optimizing the heat dissipation performance.
II. Chemical Resistance
Problems:
Home appliances are frequently exposed to a diverse range of chemicals. In a washing machine, detergents, bleaches, and water with varying chemical compositions are prevalent. In a refrigerator, there may be contact with food acids and condensation. Absent chemical resistance in the FPC material, it can corrode, leading to a diminution in conductivity, insulation breakdown, or physical damage to the circuit.
Avoidance and Suggestions:
Coating and Lamination: Apply chemical-resistant coatings or laminates over the FPC. For example, a conformal coating can safeguard the circuit from moisture and chemical vapors. Fluoropolymer coatings, such as PTFE (Polytetrafluoroethylene), are esteemed for their outstanding chemical resistance and can be deployed in applications where exposure to harsh chemicals is anticipated. Laminating the FPC with a protective layer that is inert to common household chemicals, like an epoxy resin laminate with chemical-resistant additives, can also augment its durability.
Material Compatibility Testing: Prior to finalizing the FPC material, conduct comprehensive compatibility tests with the chemicals likely to be encountered in the appliance's milieu. This encompasses testing the material's response to different pH levels, solvents, and detergents. Based on the test outcomes, select the most suitable material or institute modifications to the extant material to enhance its chemical resistance. Employing accelerated aging tests in a simulated chemical environment can provide valuable data on the long-term performance of the FPC material.
III. Flexibility and Durability
Problems:
Some home appliances feature moving parts or necessitate FPCs to be installed in areas where they are subject to repeated bending or mechanical stress. For example, the hinges of a laptop-style microwave oven door or the adjustable trays in a refrigerator. If the FPC material lacks sufficient flexibility and durability, it may develop cracks, breaks, or fatigue over time, culminating in intermittent electrical connections or complete failure.
Avoidance and Suggestions:
Choosing Flexible Materials: Opt for materials that possess inherent flexibility and can withstand repeated bending. PI is not only favorable for high-temperature resistance but also proffers reasonable flexibility. Additionally, certain elastomeric materials or composites can be harnessed in conjunction with the FPC to enhance its flexibility and shock-absorbing capabilities. For instance, embedding a thin layer of silicone rubber within the FPC structure can improve its resilience to mechanical stress. Employing flexible copper foils with enhanced elongation properties can also contribute to the overall flexibility of the FPC.
Reinforcement and Structural Design: Incorporate reinforcement elements such as fiberglass or aramid fibers in the FPC to augment its tensile strength and durability. The layout and orientation of these reinforcement materials can be optimized based on the anticipated stress directions. In areas of high bending stress, such as the hinge region, adopt a more flexible and durable design approach, like a multi-layered or segmented FPC structure that can better adapt to the mechanical movements. Utilizing stress relief features, such as rounded corners and stepped transitions, can mitigate stress concentrations and enhance the FPC's fatigue life.
IV. Electrical Conductivity and Insulation
Problems:
The FPC must exhibit good electrical conductivity to ensure efficient signal transmission and power distribution. However, it also requires proper insulation to preclude short circuits and electrical leakage. If the conductive materials possess poor adhesion or the insulation layer is defective, it can engender electrical failures and safety hazards.
Avoidance and Suggestions:
Conductive Material Selection: Use high-quality copper foils with excellent adhesion properties. The purity and thickness of the copper foil can impact its conductivity. For applications demanding high current-carrying capacity, thicker copper foils may be requisite. Ensure that the copper foil is appropriately bonded to the substrate to prevent delamination, which could result in an increase in resistance or open circuits. Employing adhesives with high peel strength and thermal stability can enhance the bond between the copper foil and the substrate.
Insulation Layer Optimization: Select insulation materials with high dielectric strength and low dielectric loss. The thickness and uniformity of the insulation layer should be meticulously controlled. For example, using a high-quality polyimide film as the insulation layer and ensuring its proper lamination and curing can enhance the insulation performance of the FPC. Regular quality checks of the insulation layer, such as insulation resistance testing using a megohmmeter and dielectric breakdown voltage testing, can help in detecting any potential defects early. Implementing quality control procedures during the lamination process, such as monitoring temperature, pressure, and curing time, can ensure the consistency and reliability of the insulation layer.
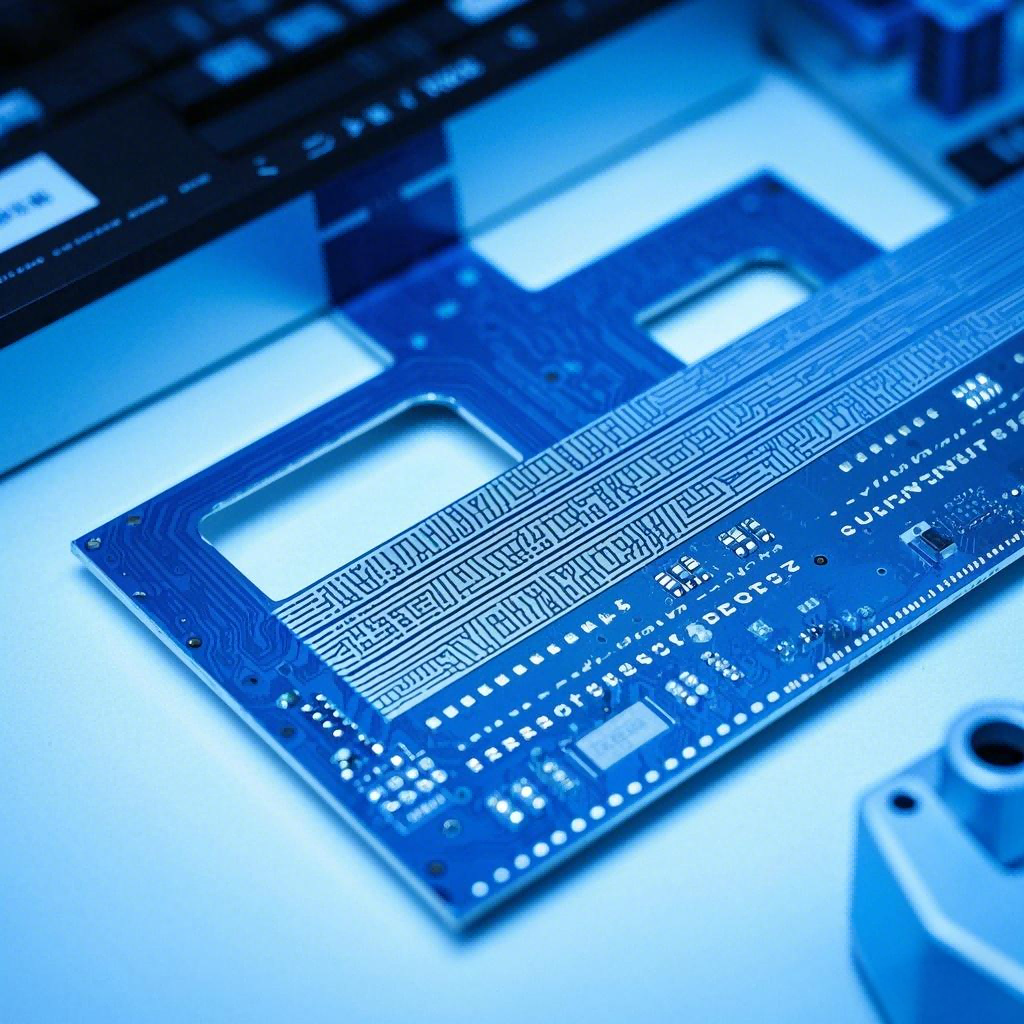
Shenzhen Huaruixin Electronics Co., Ltd. is dedicated to furnishing high-quality FPC solutions for home appliances. By scrupulously considering these material selection factors and implementing the proffered avoidance measures, manufacturers can enhance the performance and reliability of their home appliance products. We welcome our customers to engage in discussions and consultations to further explore the optimal material choices and FPC designs for their specific home appliance applications.