In the dynamic realm of electronics manufacturing, the production of custom HDI (High-Density Interconnect) first and second order multilayer rigid-flex PCBs integrated with impedance and shielding films represents the pinnacle of technological sophistication.
Shenzhen Huaruixin Electronics Co., Ltd., a renowned FPC (Flexible Printed Circuit) production and sales powerhouse, has amassed a wealth of experience in this domain. Let's dissect the essential technical nuances that demand our utmost attention.
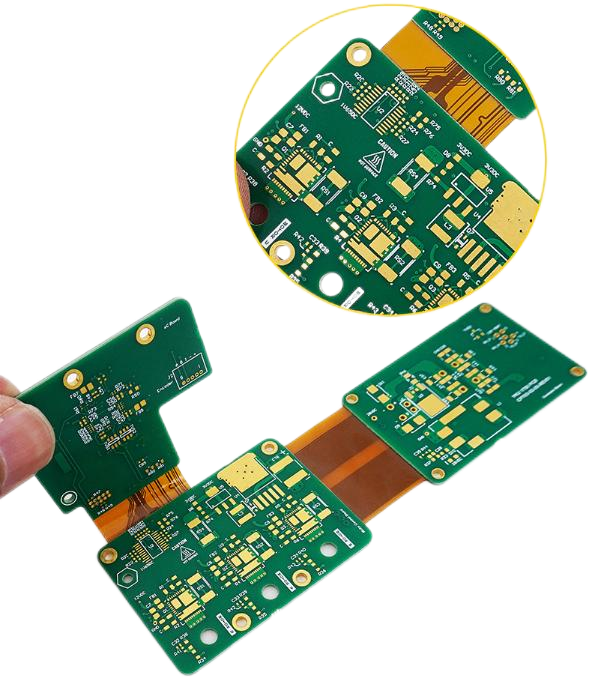
1. Design Alchemy: Balancing Complexity and Functionality
The blueprint of the PCB is the cornerstone. Engineers must engage in a delicate dance of trace routing, leveraging advanced CAD (Computer-Aided Design) tools to optimize for impedance. This entails meticulous calculations of trace impedance based on electromagnetic field theories and employing simulation software like HSPICE or ADS to predict signal behavior. In high-frequency applications, differential pair routing and proper ground plane design are not mere luxuries but necessities to curtail crosstalk and ensure signal fidelity.
2. Material Curation: The Foundation of Electrical Excellence
Selecting appropriate materials is an art in itself. Dielectric substrates with low dissipation factors and controlled dielectric constants, such as Rogers laminates, are prime candidates for impedance-critical designs. The shielding film material, be it copper foil or conductive polymers, must exhibit excellent shielding attenuation characteristics. For rigid-flex PCBs, the choice of flexible materials like polyimide with high-temperature resistance and tensile strength is non-negotiable to endure the rigors of bending and environmental stress.
3. Impedance Precision: The Quest for Signal Purity
Achieving pinpoint impedance accuracy is a herculean task. The etching process demands strict control over etch rate and uniformity using state-of-the-art etching equipment. Plating, whether it's electrolytic or electroless, must adhere to precise thickness specifications, monitored by advanced thickness measurement techniques like X-ray fluorescence. During lamination, the application of pressure and temperature profiles needs to be calibrated with precision, often relying on thermal-couple feedback and pressure sensors to ensure consistent dielectric thickness and impedance stability.
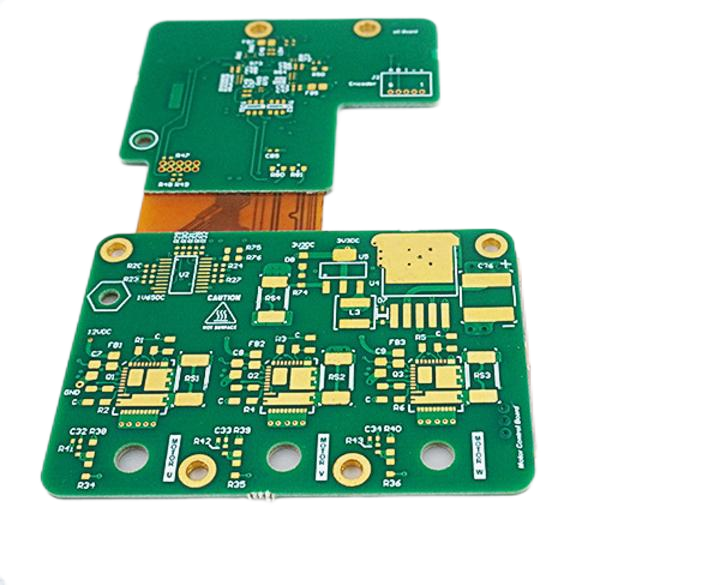
4. Shielding Film Mastery: A Barrier Against Electromagnetic Intruders
The flawless application of the shielding film is a make-or-break factor. Adhesive technologies, such as acrylic or epoxy-based adhesives, must provide robust bonding without compromising the film's shielding integrity. The grounding of the shielding film, whether through vias or conductive adhesives, must form a seamless EMI dissipation pathway. Any discontinuity in this shield can open the floodgates to electromagnetic interference, wreaking havoc on the PCB's performance.
5. Manufacturing Micro-Management: Precision at Every Step
The manufacturing floor is a theater of precision. Micro-drilling operations for vias require ultra-high precision CNC (Computer Numerical Control) machines with spindle speeds and feed rates optimized for minimal burr formation and accurate hole positioning. Solder paste printing and reflow soldering processes must be fine-tuned, with parameters like stencil thickness, solder paste viscosity, and reflow temperature profiles calibrated to the minutest detail to prevent soldering defects. In the lamination process, alignment jigs and optical alignment systems are deployed to ensure layer-to-layer registration within micrometer tolerances.
6. Quality Assurance Fortress: Rigorous Testing and Inspection Regimes
A multi-faceted quality assurance framework is the final bulwark. Impedance analyzers, such as network analyzers, are employed for impedance spectroscopy at various frequencies. AOI systems with high-resolution cameras and advanced image processing algorithms scour the PCB surface for visual defects. Electrical testing suites, including flying probe testers and boundary scan testers, perform comprehensive electrical integrity checks. Functional testers, often custom-designed for specific PCB applications, validate the board's performance under real-world operating conditions.
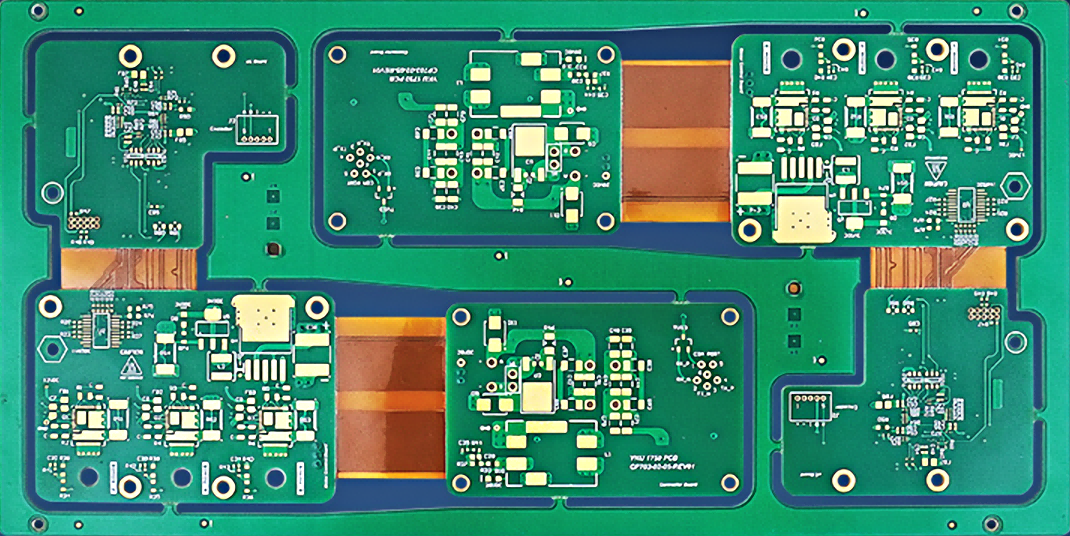
In summation, the fabrication of custom HDI multilayer rigid-flex PCBs with impedance and shielding films is a symphony of technical prowess.
Shenzhen Huaruixin Electronics Co., Ltd. stands at the forefront, ready to collaborate with clients in orchestrating this complex manufacturing ballet and delivering PCBs that set new benchmarks in the electronics industry.