Key Considerations in the Production of FPC for Batteries: Design, Manufacturing, Quality Control, and Packaging
- Dec 19,2024
-
Share
Flexible Printed Circuits (FPCs) have emerged as the unsung heroes in modern battery applications, revolutionizing the way power is managed and connections are established within compact and sophisticated systems. Shenzhen Huaruixin Electronics Co., Ltd., a trailblazer in the FPC manufacturing and sales domain with a wealth of hands-on experience, is here to take you on an exciting journey through the intricate world of FPC production for batteries. We extend a warm invitation to both our long-standing patrons and new enthusiasts to join us in this voyage of discovery, where we will dissect every facet, from design blueprints to manufacturing finesse, quality assurance protocols, and packaging ingenuity.
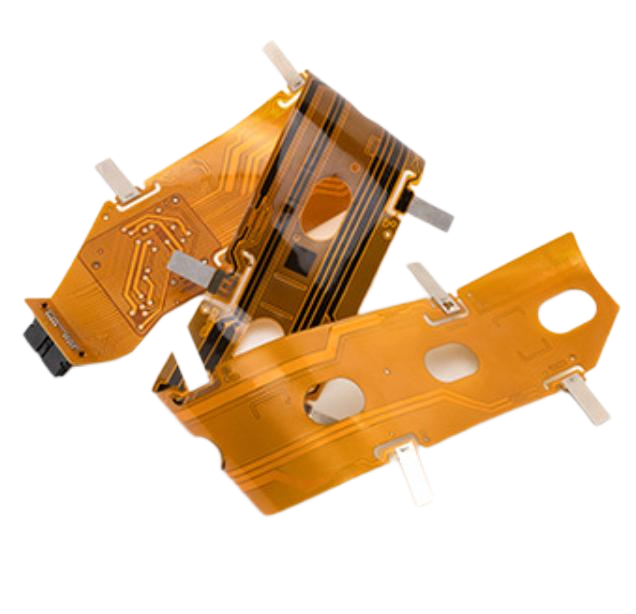
Design Phase
Material Selection: The Foundation of Excellence
The selection of the base material is a make-or-break decision. Polyimide (PI), renowned for its stellar heat resistance, chemical inertness, and mechanical pliability, takes center stage. The thickness of the PI layer is a carefully calibrated variable, tuned to the unique demands of the battery application. In high-octane battery packs that handle hefty currents and soaring temperatures, a more substantial PI layer might be the ticket to reliability.
Copper, the go-to conductor material, demands equal attention. Its thickness and purity levels are not mere technicalities but strategic choices. Thinner copper foils offer enhanced flexibility yet may cap the current-carrying capabilities. Opting for high-purity copper is the secret sauce for slashing resistance and supercharging conductivity.
Circuit Layout Design: Precision in Every Trace
Trace width and spacing are the tightrope walk of FPC design. Narrower traces are space-saving wizards but can hike resistance and hobble current flow. Adequate spacing between traces is the firewall against short circuits, especially in high-voltage battery battlegrounds. Picture a lithium-ion battery pack with a voltage rating that soars above 48V; here, a minimum trace spacing of 0.2mm or more is the golden rule.
The layout also orchestrates the symphony of connections with battery cells and other components. It's all about engineering reliable, low-resistance junctions. Plated through-holes and surface mount pads with finessed dimensions and finishes step up to the plate to ensure top-notch soldering quality.
Flexibility and Bend Radius Design: Bending without Breaking
FPCs in battery setups often need to contort and fold to snugly fit into tight quarters. The bend radius is the guardian angel that shields the conductors and insulating layers from harm. A cardinal principle is to uphold a minimum bend radius of at least 5 times the FPC's thickness. So, if the FPC is a svelte 0.2mm thick, a 1mm minimum bend radius is the charm that wards off copper trace cracks and layer delamination.
Printing and Etching: The Art of Circuit Creation
The printing ballet of the circuit pattern demands a maestro's touch in controlling ink thickness and uniformity. Cutting-edge printing techniques like screen printing or photolithography are the virtuoso tools that guarantee pinpoint pattern replication. In the photolithography spotlight, exposure time and intensity are the dials that need precise tuning to hit the bullseye of desired resolution.
Etching away the unwanted copper foil is a high-stakes act. The etching solution's composition and temperature are the variables that must be optimized to achieve a flawless, smooth etch. Over-etching is the villain that can ravage the underlying PI layer, while under-etching leaves behind pesky residual copper, throwing a wrench in circuit performance. Consider a typical copper etching concoction of cupric chloride and hydrochloric acid in a carefully balanced recipe, with the etching temperature hovering around 50°C.
Lamination: Bonding Layers in Harmony
Laminating the FPC's diverse layers – the PI substrate, conductor layer, and coverlay – is a delicate dance of alignment and pressure control. A single misstep in alignment can spawn shorts or open circuits. The lamination pressure is a bespoke setting, adjusted to the thickness and nature of the materials in play. When fusing a 0.1mm thick coverlay onto a copper-clad PI substrate, a pressure range of around 3 - 5 MPa is the sweet spot.
The curing encore after lamination is no less crucial. The temperature and time of curing are the commandments that must be religiously followed to cement proper adhesion between layers. A wrong turn in curing can unleash the chaos of delamination. Picture a typical curing temperature for epoxy-based adhesives around 150°C for a 60 - 90 minute curing time.
Drilling and Plating: Precision Punctures and Plating Perfection
Drilling holes for component mounting or vias is a precision sport. The drill bit's size and speed are the weapons of choice, selected with surgical precision based on the hole diameter and the material being drilled. When boring a 0.3mm diameter hole in a PI substrate, a drill bit with a diameter tolerance of ±0.01mm and a rotational speed of around 100,000 - 150,000 RPM is the ace up the sleeve.
Plating the drilled holes with conductive copper is the linchpin for rock-solid electrical connections. Plating thickness and uniformity are the benchmarks that must be nailed. A plating thickness of 10 - 20 microns is the gold standard for conductivity and solderability. The plating process parameters, like current density and plating time, are the levers that need fine-tuning.
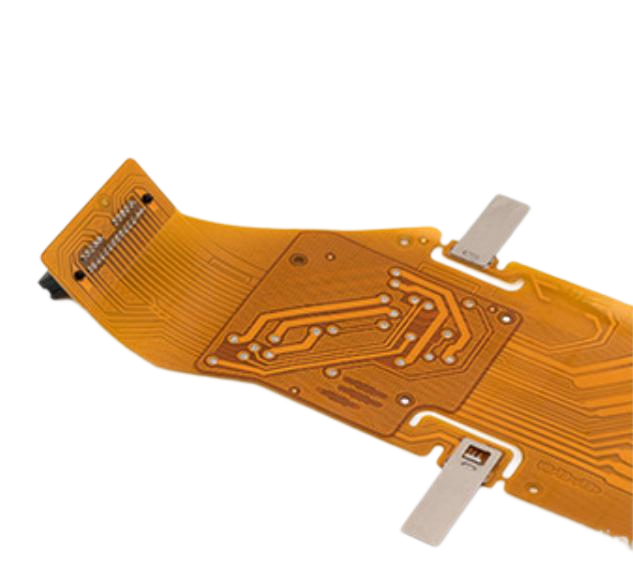
Visual Inspection: The Eagle-Eyed Scrutiny
Trained inspectors morph into detectives, conducting a painstaking visual inspection of the FPCs. They scour for any telltale signs of imperfection – scratches, dents, or color aberrations on the surface. The alignment of circuit patterns and the integrity of solder masks are also under the microscope. Any scratch deeper than 5 microns or a circuit feature misalignment exceeding 0.1mm is a red flag.
The inspection spotlight also shines on connection points, ensuring no lifted pads or broken traces escape detection. Magnification tools like microscopes with a 10x - 50x zoom are the magnifying glasses that help unearth these minute flaws.
Electrical Testing: Probing for Electrical Integrity
Conductivity testing is the litmus test for verifying the health of electrical pathways. Armed with multimeters or specialized continuity testers, the resistance between different FPC points is measured and cross-checked against design specs. In a power distribution FPC, the resistance between input and output terminals must toe the line within a tight tolerance range, typically ±5% of the designed resistance.
Insulation resistance testing is the shield against leakage currents, especially in high-voltage battery arenas. The insulation resistance between different conductive layers and traces is the metric that matters. A minimum insulation resistance of 100 megohms or more is the bulwark that keeps leakage at bay.
Reliability Testing: Stress-Testing for Durability
Bend testing is the endurance trial that gauges the FPC's flexibility and staying power. The FPC is put through its paces, repeatedly bent to a set bend radius and a specified number of cycles, then examined for any battle scars like cracks or breaks in the conductors. In a battery application where the FPC might endure 1000 bends in its lifetime, a sample FPC is put to the test for at least 2000 - 3000 cycles to prove its mettle.
Temperature cycling testing is the thermal rollercoaster that mimics the real-world temperature swings an FPC faces in battery operation. The FPC is plunged into a temperature range, typically from -40°C to +85°C, and then inspected for any signs of delamination or electrical property mutations. The number of temperature cycles can vary from 100 - 500, depending on the application's demands.
Packaging Materials Selection: Shielding from the Elements
Anti-static packaging materials are the FPC's bodyguards against electrostatic discharge (ESD) damage. Think anti-static bags or trays crafted from polyethylene terephthalate (PET) with an anti-static cloak. These packaging materials also double as armor against scratches and impacts.
Desiccants are the humidity busters slipped into the packaging. Excessive moisture is the enemy that can rust the copper conductors and cripple solderability. Silica gel desiccants are the trusty sidekicks, with their quantity calculated based on the packaging volume and the desired humidity control level.
Packaging Design: A Cozy and Informed Cocoon
The FPCs are nestled and secured within the packaging to avoid any jostling during transit. Foam inserts or plastic holders are the cushions that keep them in place. The packaging design also has the end-user in mind, ensuring easy unpacking and handling.
Clear labeling on the packaging is the FPC's identity card. It spills the beans on details like the part number, quantity, manufacturing date, lot number, and any special handling instructions. If the FPC has a magnetic phobia, a label screaming "Keep away from magnets" is slapped on.
Shipment Considerations: A Smooth Sailing to the Destination
The shipping method is a strategic choice, hinged on the FPC's urgency and delicacy. For high-value or time-sensitive FPCs, express shipping might be the express lane. But shock and vibration protection measures are non-negotiable. Bubble wrap or foam padding are the shock absorbers that minimize transit damage risks.
Shipment documentation, including invoices, packing lists, and relevant certificates (like RoHS compliance certificates), must be letter-perfect. This is the passport that ensures a seamless customs clearance and a hitch-free delivery journey.
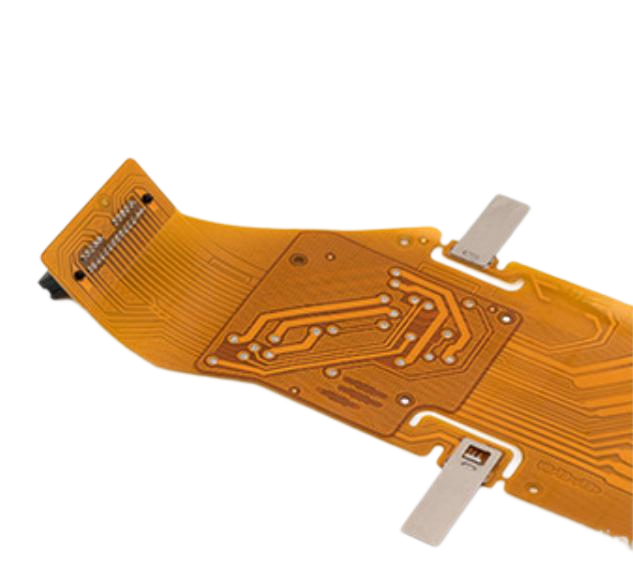
In a nutshell, the production of FPCs for batteries is a riveting blend of art and science. Meticulous attention to every detail in design, manufacturing, quality control, and packaging is the recipe for ensuring the FPCs' sterling performance and long-term durability in battery applications.
Shenzhen Huaruixin Electronics Co., Ltd. stands at the forefront, armed with the expertise and experience to meet and exceed the market's kaleidoscopic needs. We are eager to join forces with customers and partners, forging ahead in the FPC frontier and scripting a story of innovation and excellence