Key Considerations and Solutions in the Design and Production of FPCs for Vehicle Infotainment Systems
- Dec 20,2024
-
Share
In the automotive industry, the vehicle infotainment system has become a crucial component, enhancing the driving experience. Flexible Printed Circuits (FPCs) play a vital role in connecting the display, touch panel, and multimedia interfaces. Shenzhen Huaruixin Electronics Co., Ltd., with its extensive experience in FPC manufacturing and sales, is well-versed in handling the unique challenges associated with these applications. We welcome new and existing customers to engage in discussions and knowledge sharing.
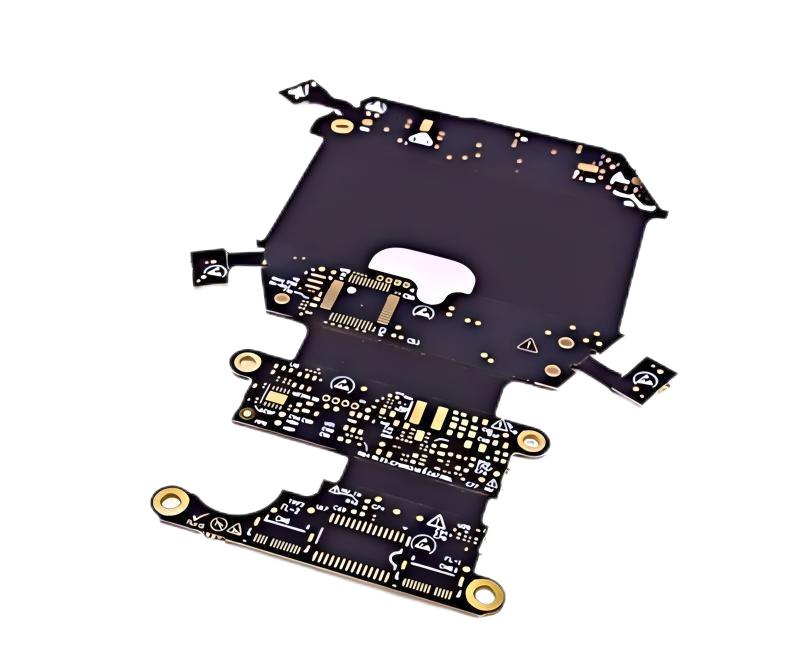
Design Phase Considerations and Solutions
Problem: In a vehicle infotainment system, high-speed signals are transmitted between different components. Ensuring signal integrity and minimizing EMI is crucial as the automotive environment is rife with various electronic systems that can cause interference. For example, if EMI is not properly controlled, it can lead to distorted images on the display or erratic touch panel responses.
Solution: We use differential pairs for high-speed signal transmission. The traces are carefully designed with controlled impedance, typically around 100 ohms. To reduce EMI, a ground plane is incorporated adjacent to the signal layers. In one of our projects for a leading automotive brand's infotainment system, we implemented a 4-layer FPC design. The inner layers consisted of power and ground planes, which provided shielding and stable power distribution. The outer layers were dedicated to signal traces. By optimizing the trace widths, spacing, and layer stack-up, we were able to achieve excellent signal integrity and EMI suppression. The system passed all the required electromagnetic compatibility (EMC) tests.
Problem: The automotive environment subjects FPCs to a wide range of temperatures, from extremely cold (-40°C) during winter starts to hot conditions (up to +85°C) in a parked vehicle under the sun. Additionally, vibrations and mechanical stresses from the vehicle's movement can cause damage to the FPC over time.
Solution: We select materials with high-temperature resistance, such as polyimide (PI) with a thermal rating suitable for automotive applications. The copper conductors are also chosen for their durability and resistance to thermal expansion. For example, in a recent production run for a vehicle infotainment FPC, we used a 50-micron thick copper foil on a 25-micron thick PI substrate. To enhance durability against vibrations, we incorporated stiffeners at critical points, like the connector areas. These stiffeners were made of a rigid yet lightweight material and were carefully attached to the FPC without affecting its flexibility in other areas. The FPC was then subjected to extensive temperature cycling and vibration testing. After 1000 cycles of temperature variation and several hours of vibration testing equivalent to the vehicle's lifetime stress, the FPC showed no signs of delamination, cracks, or electrical performance degradation.
Problem: The interior of a vehicle dashboard has limited space, and FPCs need to be routed and bent to fit into tight areas while maintaining functionality. A small bend radius can cause conductor cracking and layer delamination if not properly designed.
Solution: We use advanced design software to optimize the layout of the FPC, minimizing its overall size. The bend radius is carefully calculated and designed to be at least 5 times the thickness of the FPC. For instance, in a project where the FPC had a thickness of 0.2mm, the minimum bend radius was set to 1mm. To further enhance flexibility, we incorporated flexible coverlays and used a stepped or curved design in areas where the FPC needed to make sharp turns. This allowed the FPC to fit snugly into the available space without compromising its reliability. The final design was tested in a mock-up of the vehicle dashboard, ensuring that it could be installed without any interference and still function properly.
Problem: The complex design of FPCs for vehicle infotainment systems requires high precision in manufacturing. Any errors in printing, etching, lamination, or drilling can lead to defective products.
Solution: We employ state-of-the-art manufacturing equipment with high precision capabilities. For example, our photolithography machines have a resolution of up to 25 microns, ensuring accurate circuit pattern transfer. During the etching process, we closely monitor the etching solution composition and temperature. The etching solution is regularly analyzed and adjusted to maintain the optimal etch rate and quality. In the lamination process, we use automated alignment systems with an accuracy of ±0.05mm to ensure proper layer alignment. After production, a comprehensive quality control process is implemented. Visual inspection is carried out using high-magnification microscopes to detect any surface defects. Electrical testing includes continuity testing, insulation resistance testing, and impedance measurement. In a batch of 1000 FPCs produced for a vehicle infotainment system, our strict quality control measures resulted in a defect rate of less than 0.5%, well below the industry average.
Problem: The FPC needs to connect reliably to various connectors in the infotainment system, such as those for the display, touch panel, and multimedia interfaces. Any issues with the connector interface can lead to intermittent connections or complete failures.
Solution: We work closely with connector manufacturers to ensure proper design compatibility. The FPC's connector pads are designed with the correct dimensions and finishes to match the connectors. For example, we use gold plating on the connector pads to enhance conductivity and corrosion resistance. During production, we conduct pull and push force tests on the connectors to ensure a secure fit. In a particular project, we had to interface the FPC with a new type of miniaturized connector. We collaborated with the connector supplier to develop a custom pad design. After extensive testing, the connector interface passed all the required reliability tests, including shock and vibration testing while maintaining a stable electrical connection.
In conclusion, the design and production of FPCs for vehicle infotainment systems require a deep understanding of the unique requirements and challenges of the automotive environment.
Shenzhen Huaruixin Electronics Co., Ltd. has the expertise and experience to overcome these hurdles and deliver high-quality FPCs. We look forward to collaborating with customers and partners to further advance the technology and performance of FPCs in vehicle infotainment applications.