Ensuring the Reliability and Stability of FPC in VR/AR Devices: A Comprehensive Guide
- Dec 31,2024
-
Share
In the dynamic realm of Virtual Reality (VR) and Augmented Reality (AR) technology, the Flexible Printed Circuit (FPC) stands as a linchpin for the seamless operation and optimal performance of these cutting-edge devices. The integrity of FPCs is not only essential for the functionality but also for the overall user experience in this rapidly evolving field.
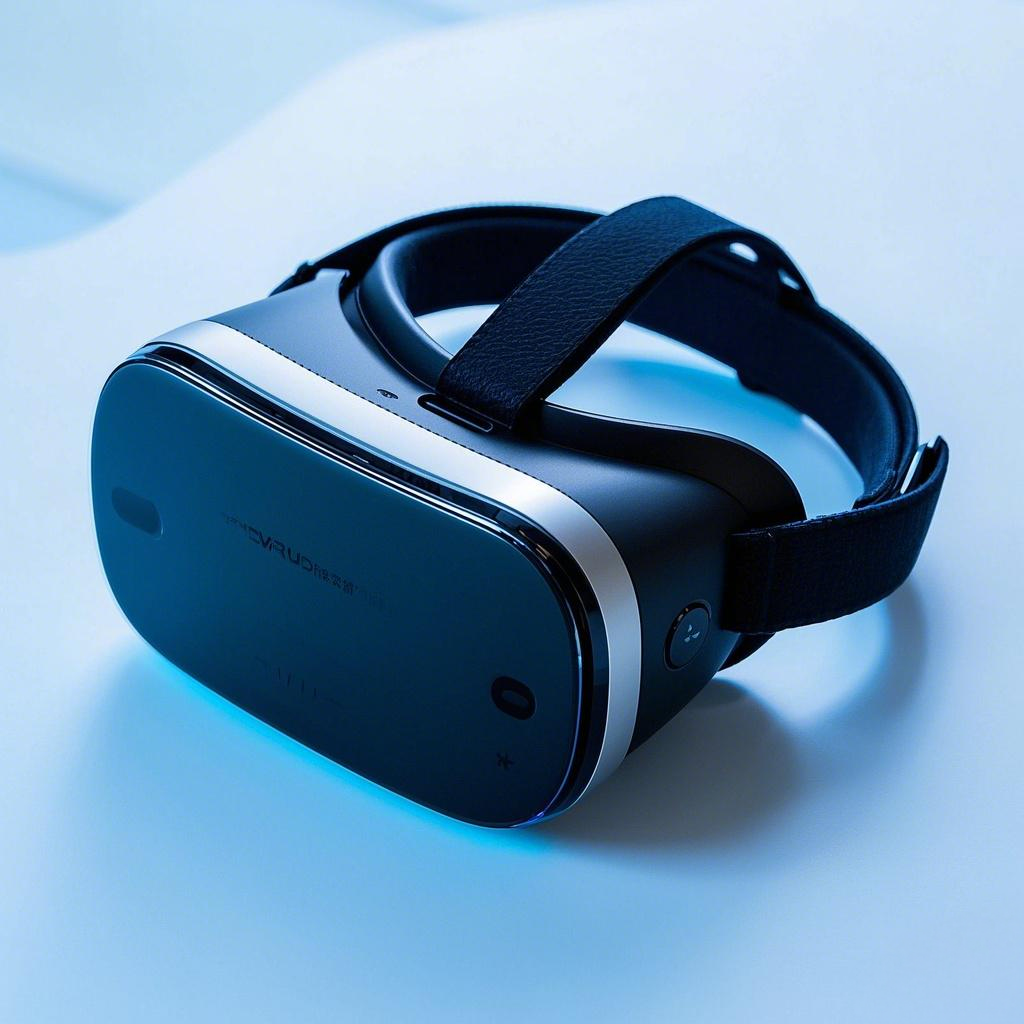
1. Meticulous Design Engineering
Sophisticated Layout Strategies: Crafting an FPC layout within VR/AR devices demands precision and foresight. Given the confined spaces and complex architectures of these gadgets, every millimeter counts. Engineers must navigate the intricate geometries to ensure that the FPC is artfully routed, dodging potential interference with critical components such as high-resolution displays, sensitive sensors, and power-dense batteries. For instance, in a state-of-the-art VR headset, the FPC interconnecting the micro-OLED display panel to the main processing board requires a layout that not only maximizes space utilization but also mitigates the risk of signal crosstalk and electromagnetic interference. This entails leveraging advanced Computer-Aided Design (CAD) tools and simulation software to predict and preempt any potential pitfalls during the device's operation.
Redundancy Architectures for Resilience: Incorporating redundancy into the FPC design paradigm is a non-negotiable aspect of enhancing its reliability. Critical signal pathways can be duplicated or triplicated, implementing a fail-safe mechanism. In scenarios where a primary line succumbs to physical stress-induced fractures or electrical anomalies like short circuits, the redundant lines instantaneously assume the signal transmission duties. This redundancy is of utmost importance in mission-critical AR applications, such as those deployed in industrial automation, surgical navigation, or military training simulations, where uninterrupted operation is not a luxury but a necessity.
Thermal Management Integration: VR/AR devices are notorious for generating substantial heat during operation, and this thermal load can pose a significant threat to the performance and longevity of the FPC. The design phase must factor in the proximity and thermal dissipation characteristics of heat-emitting components like high-performance Application-Specific Integrated Circuits (ASICs) and power-hungry Graphics Processing Units (GPUs). Selecting base materials with enhanced thermal conductivity and heat resistance, such as advanced polyimide formulations, is a starting point. Additionally, integrating thermal vias, heat spreaders, or even phase-change materials within the FPC structure can effectively dissipate heat, preventing overheating-induced degradation of the FPC's electrical and mechanical properties over time.
2. Prudent Material Selection
Premium Base Material Attributes: The choice of the base material for the FPC is a cornerstone decision. Polyimide (PI) reigns supreme in this domain, renowned for its outstanding flexibility and thermal stability. It can endure the incessant bending, twisting, and folding that FPCs are subjected to in the ergonomic usage scenarios of VR/AR devices. When a user casually adjusts the position of a sleek wearable AR device, the FPC connecting disparate modules must possess the resilience to flex without succumbing to cracking or compromising its electrical conductivity. High-grade PI materials, characterized by consistent thickness profiles and exceptional flexibility retention, are indispensable for ensuring reliable and long-term performance.
Conductor Material and Surface Finishes: Copper, with its excellent electrical conductivity, is the de facto choice for FPC conductors. However, the devil is in the details. The purity and thickness of the copper foil must be meticulously calibrated. High-purity copper not only offers lower resistivity, minimizing signal attenuation during transmission but also contributes to enhanced current-carrying capacity. Moreover, the application of appropriate surface finishes such as tin or gold plating is not a mere embellishment but a critical step. These finishes augment the solderability of the copper conductors, ensuring robust and reliable connections to other components. They also confer enhanced resistance to oxidation, a common nemesis in the often-humid and temperature-fluctuating operating environments that VR/AR devices inhabit.
3. Exacting Manufacturing Process Oversight
Precision Fabrication Techniques: The manufacturing of FPCs is a high-precision ballet. Advanced photolithography and etching processes are harnessed to etch intricate and precise circuit patterns with micron-level accuracy. Stringent control over the etching parameters, such as etchant concentration, temperature, and exposure time, is imperative to guarantee that the line widths and spaces adhere to the exacting design specifications. This level of precision is the bulwark against short circuits and a guarantor of signal integrity. In the context of high-density FPCs powering the next-generation VR/AR displays with pixel densities exceeding the human eye's resolving power, the line widths can dwindle to a few micrometers. Any deviation in the etching process, no matter how minute, could precipitate catastrophic performance failures.
Multi-Tiered Quality Inspection Regime: A battery of quality inspection protocols is instituted at every stage of the manufacturing process. Visual inspections, aided by high-magnification optical microscopy and automated vision systems, are deployed to detect any physical imperfections, be it microscopic scratches, dents, or incomplete etching. Electrical tests, encompassing insulation resistance measurements, continuity checks, and impedance spectroscopy, are conducted to validate the proper functioning of the circuits. Complementing these are reliability tests that mimic the real-world operating conditions, including temperature cycling between sub-zero and elevated temperatures, humidity exposure tests, and mechanical flexing endurance tests. Only FPCs that emerge unscathed from these rigorous quality sieves are deemed worthy of integration into the final VR/AR device assembly.
4. Adroit Assembly and User-Centric Usage Protocols
Expert Assembly Methodologies: During the assembly of VR/AR devices, a team of highly trained technicians, armed with specialized tools and calibrated skills, must handle the FPC with the utmost delicacy. They must adhere to meticulously documented procedures for inserting and connecting the FPC to its mating components. This involves using ergonomic insertion tools and applying a calibrated amount of force to ensure a snug and secure connection without inflicting any damage to the FPC or its connectors. For example, when mating an FPC connector to its receptacle, it demands a precise alignment and a gentle, yet firm insertion to preclude intermittent connections or damage to the delicate connector pins.
User Empowerment and Device Safeguarding: Equipping the end-users with comprehensive usage instructions is an equally important facet of ensuring the FPC's longevity. Users should be enlightened about the correct handling techniques to avert excessive stress on the FPC. This can encompass guidelines on how to gracefully don and doff wearable devices, eschewing any abrupt or violent movements that could subject the FPC to bending or twisting beyond its engineered limits. Additionally, the device design can incorporate innovative protective features such as flexible and shock-absorbent covers, or abrasion-resistant shields encasing the FPC, safeguarding it from accidental impacts, scratches, and abrasions during the vicissitudes of normal use.
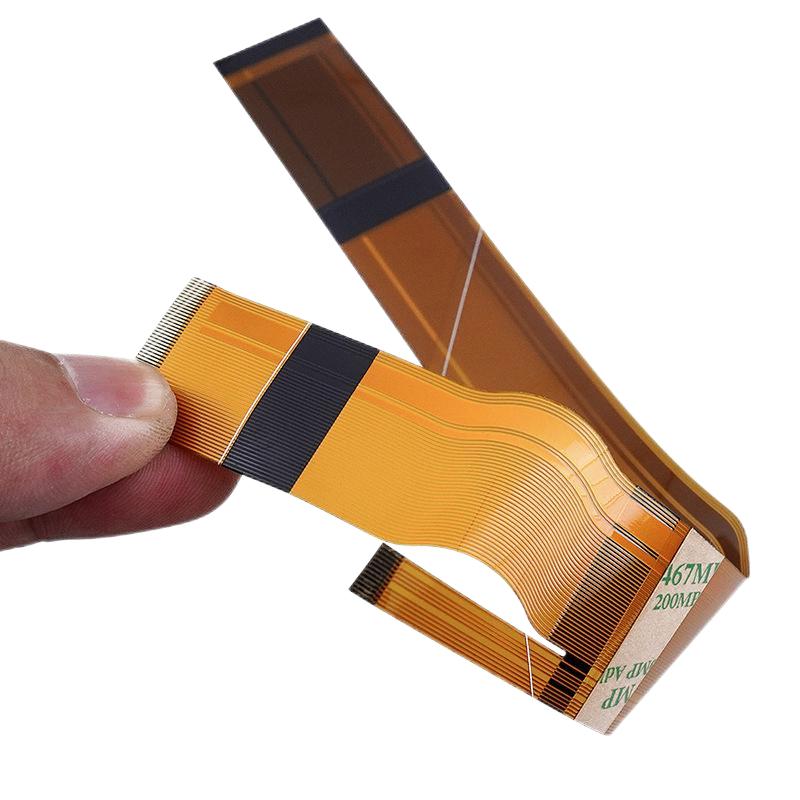
In conclusion, safeguarding the reliability and stability of FPCs in VR/AR devices mandates a holistic and multi-faceted approach. It traverses the domains of design ingenuity, material acumen, manufacturing precision, and user education. By implementing these strategies with unwavering commitment, manufacturers can supercharge the overall performance and durability of VR/AR devices, thereby elevating the user experience to new zeniths.
Here at Shenzhen Huaruixin Electronics Co., Ltd., we pride ourselves on being a vanguard in the professional design and production of top-tier FPCs tailored specifically for the VR/AR industry. Our team of seasoned engineers and technicians brings to the table a wealth of experience and technical prowess, leveraging state-of-the-art technologies and adhering to the most stringent quality standards. We are dedicated to forging reliable and high-performance FPCs that not only meet but exceed the exacting requirements of this burgeoning field.
We extend a warm invitation to both our long-standing partners and new acquaintances in the VR/AR ecosystem to engage in fruitful discussions and collaborations. Let us join forces to scale new heights, pioneer innovative solutions, and drive the continued evolution of VR/AR technology. Together, we can shape the future of immersive experiences and redefine the boundaries of what is possible.