Ensuring Quality and Reliability of FPCs in Medical Monitoring Devices and Their Application Advantages
- Dec 23,2024
-
Share
In the intricate domain of medical technology, Flexible Printed Circuits (FPCs) have emerged as a cornerstone in medical monitoring devices. However, guaranteeing the quality and reliability of FPCs within such critical applications demands meticulous attention and a multi-faceted approach.
I. Ensuring Quality and Reliability of FPCs in Medical Monitoring Devices
A. Design Phase
Accurate Requirement Analysis
A profound and in-depth comprehension of the specific functional exigencies of medical monitoring devices is non-negotiable. For instance, in an electrocardiogram (ECG) apparatus, parameters like signal resolution and sampling frequency must be meticulously defined. These parameters directly impinge upon the circuit layout of the FPC, dictating aspects such as the width and pitch of signal traces to ensure the unerring transmission of feeble ECG waveforms.
The consideration of the device's operational milieu is equally vital. In the case of a portable medical monitoring gizmo earmarked for field first aid, the FPC must possess the resilience to withstand temperature and humidity fluctuations as well as potential mechanical shocks. During the design phase, judicious selection of materials and configurations is imperative to align with these environmental stipulations.
Reasonable Circuit Design
Optimization of the circuit topology is essential to curtail signal interference. In medical monitoring contraptions, signal fidelity is sacrosanct. For example, within a blood glucose meter, the sensor signal routing must be maintained at a suitable clearance from other potentially interfering conductors (such as power buses), and appropriate grounding modalities, be it single-point or multi-point grounding, should be implemented in consonance with the specific signal frequency spectrum and device requisites to mitigate electromagnetic interference (EMI) and crosstalk.
Rigorous circuit simulation and validation procedures are requisite. Sophisticated circuit design software is harnessed to model the FPC circuitry and scrutinize pivotal parameters like signal integrity and timing. For instance, during the design of an FPC for a blood pressure monitoring apparatus, the transmission characteristics of the blood pressure sensor signal are simulated to ascertain its unblemished conveyance to the processing chip across diverse operating frequencies and loading scenarios.
Appropriate Material Selection for Medical Applications
Substrate material selection is a critical determinant. Materials endowed with sterling biocompatibility, chemical inertness, and mechanical robustness are the materials of choice. Polyimide (PI) substrates, for example, are prevalently utilized due to their remarkable high-temperature tolerance, a certain degree of chemical resistance, and compliance with the biocompatibility norms mandated by medical devices, thereby precluding any untoward effects on patients.
The choice of conductive materials is equally consequential. For the copper foil constituting the conductive stratum, products exhibiting high purity and tenacious adhesion are imperative. High-purity copper foil vouchsafes excellent electrical conductivity, while robust adhesion precludes the detachment of the copper foil during service, safeguarding circuit continuity. Additionally, for select medical devices with idiosyncratic demands, alternative conductive media such as silver paste might be contemplated to satiate more exacting signal transmission prerequisites.
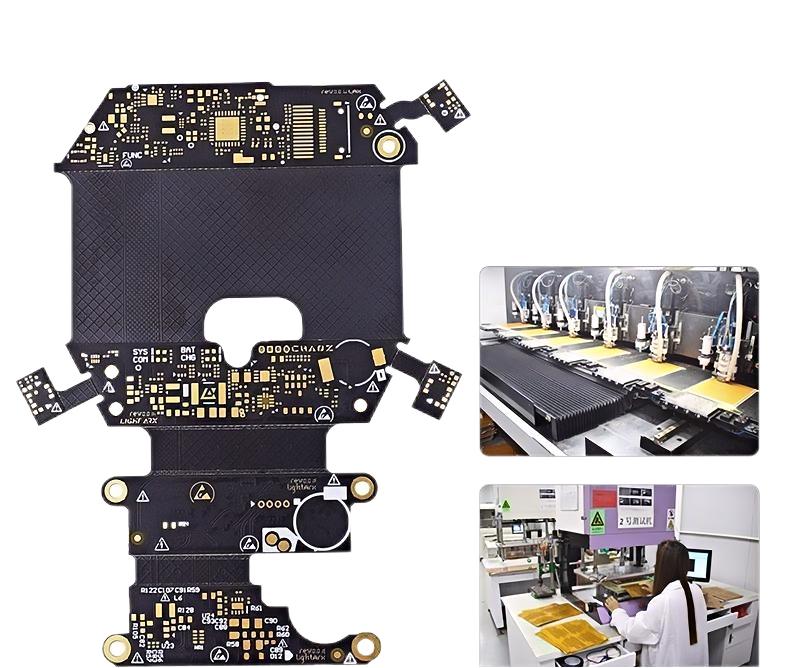
B. Production and Manufacturing Phase
Strict Raw Material Inspection
Stringent inspection protocols are instituted for each batch of substrate materials, conductive foils, adhesives, and other raw constituents. The thickness, planarity, mechanical attributes, and other benchmarks of the substrate are meticulously verified to ensure congruence with design specifications. For example, in an FPC with stringent thickness tolerances, any significant deviation in substrate thickness could compromise the overall flexibility and assembly precision of the FPC.
The electrical characteristics of conductive materials, encompassing resistivity and corrosion resistance, are subject to exhaustive testing. Specialized testing apparatuses like four-point probe testers are deployed to gauge the resistivity of copper foil, ensuring its optimal electrical conductivity. Moreover, salt spray tests and other corrosion assays are carried out to appraise its resistance to chemical degradation, given the potential exposure to a gamut of chemical substances in the medical environment.
High-Precision Manufacturing Process Control
Etching process control is a linchpin in FPC fabrication. Parameters such as etching solution concentration, etching duration, and temperature must be calibrated with pinpoint precision to ensure the fidelity of the circuit traces. In the production of FPCs for medical imaging apparatuses, where circuit precision is of the essence, even a minuscule etching aberration could precipitate signal transmission anomalies. Hence, high-precision etching equipment and exacting process parameter controls are sine qua non.
Lamination process optimization is equally pivotal. During lamination, it is incumbent upon manufacturers to ensure seamless bonding between layers, devoid of any voids or bubbles. In the manufacture of FPCs for implantable medical monitoring devices, any interlayer imperfections could precipitate device malfunction. Consequently, factors like lamination pressure, temperature, and time must be stringently regulated, and top-tier adhesives must be employed.
Comprehensive Quality Inspection System
Appearance inspection is a crucial checkpoint. Microscopic examination and other visual inspection techniques are employed to detect flaws such as short circuits, open circuits, incomplete etching, and pinholes. In the context of FPCs for medical monitoring devices, these cosmetic blemishes could engender signal transmission glitches or outright device failures. Ergo, stringent quality control measures are indispensable.
Electrical performance testing is comprehensive and exhaustive. Specialized testing paraphernalia is utilized to conduct a battery of electrical performance evaluations, including insulation resistance testing, dielectric withstand voltage testing, and signal transmission fidelity testing. For example, in medical devices, subpar insulation resistance could precipitate electrical leakage, jeopardizing patient safety. Thus, the insulation integrity of the FPC must be unimpeachable.
C. Assembly and Usage Phase
Standardized Assembly Process
Elaborate and standardized assembly guidelines are formulated for integrating FPCs into medical monitoring devices. Assembly personnel must undergo rigorous training to preclude any inadvertent damage to the FPC during the assembly process. For example, during the connection of the FPC to other electronic components, appropriate tools and correct connection methodologies must be employed to avert excessive flexing or tensile stress on the FPC, thereby forestalling trace breakage.
Immediate post-assembly functional testing is obligatory. Once the device is assembled, a comprehensive functional test is promptly carried out to ascertain the proper operation of the FPC and the accuracy of signal transmission. For example, after the assembly of a portable multi-parameter medical monitoring device, tests for ECG, blood pressure, blood oxygen, and other parameters are conducted to validate the seamless functionality of the FPC within the device.
Long-Term Reliability Monitoring
A robust device operation monitoring framework is established. After the medical monitoring device is deployed, data pertaining to its operation, inclusive of the FPC's performance metrics, are amassed through remote monitoring or regular on-site inspections. For example, in the case of bedside monitors ubiquitously deployed in healthcare facilities, their operational data is harvested via the hospital's equipment management system to prognosticate potential failure risks of the FPC.
Systematic maintenance and replacement regimens are devised. Based on factors such as device usage frequency and environmental exposure, a rational FPC maintenance and replacement schedule is formulated. For high-utilization medical monitoring devices, such as those in emergency rooms, the FPC maintenance cycle is truncated, and any defective FPCs are expeditiously detected and supplanted to ensure the uninterrupted reliability of the device.
II. Application Advantages of FPCs in Medical Monitoring Devices
High Customizability
The heterogeneous nature of medical monitoring devices, with their diverse form factors and internal architectures, renders high customizability a prized attribute of FPCs. For example, in the case of bespoke medical sensor modules with unique geometries or complex circuitry housed within constricted spaces, FPCs can be artfully contoured and wired to conform precisely, a feat that is often arduous for traditional rigid circuit boards to replicate.
Effective Heat Dissipation Management
In certain medical monitoring devices, such as high-precision imaging modalities or long-duration physiological parameter monitors, the heat dissipation quandary is a significant concern. Owing to their material constitution and structural design, FPCs are adept at dissipating heat, thereby averting the deleterious consequences of local overheating on device performance and stability. For example, through judicious engineering of the copper foil distribution and the incorporation of heat dissipation planes, FPCs can channel heat away from critical components to dedicated heat sinks, thereby prolonging the operational lifespan and enhancing the reliability of the device.
Cost-Effective Advantage
While the initial design and manufacturing outlays for FPCs might seem steep, they offer a compelling cost-benefit proposition over the long haul. As production technologies mature and economies of scale are realized, the unit cost of FPCs diminishes. Moreover, the enhanced reliability and stability of FPCs translate into reduced maintenance, replacement costs, and minimized downtime-induced indirect costs in medical monitoring devices. From a holistic life cycle perspective, FPCs present a favorable economic calculus.
Significant Weight Reduction Advantage
For portable and wearable medical monitoring devices, such as ambulatory ECG monitors and sleep apnea detectors, weight minimization is a cardinal design objective. FPCs, with their featherweight construction compared to traditional rigid circuit boards, confer a distinct advantage. By reducing the overall heft of the device, FPCs enhance patient comfort and compliance and also streamline the logistical aspects of device handling and transportation for healthcare providers.
Shenzhen Huaruixin Electronics Co., Ltd., a preeminent professional in the FPC manufacturing and sales echelon, replete with a wealth of experience, extends a warm invitation to both extant and prospective clients to engage in a fruitful dialogue and collaborative exploration in this domain.