ENIG Surface Treatment in Rigid - flex Board Production: What You Need to Know
- Nov 18,2024
-
Share
When it comes to rigid - flex board production, electroless nickel - immersion gold (ENIG) surface treatment is a key process that can greatly impact the quality of your final product. Here at Shenzhen Huaruixin Electronics Co., Ltd., a leading FPC production and sales company, we want to share with you the important aspects of ENIG - its advantages, common mistakes to avoid, and some real - world success stories.
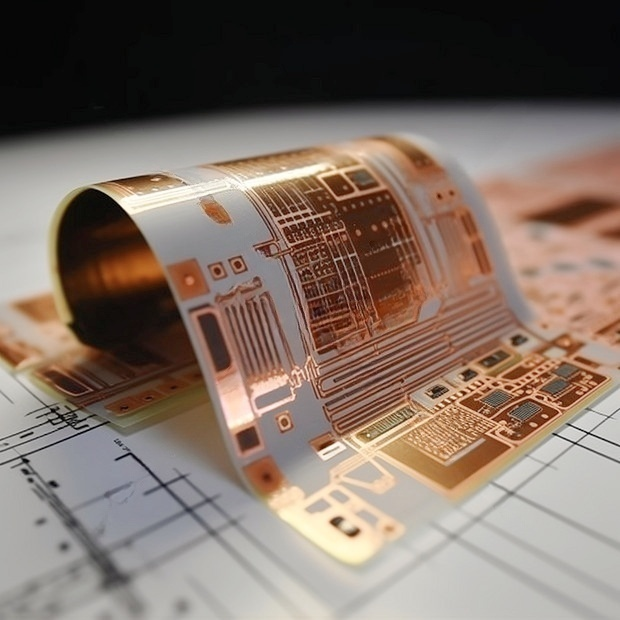
Why ENIG is Great
1. Top - Notch Solderability and Wire Bonding
ENIG gives you a beautiful, flat gold surface that's a dream for soldering. If you have components with really fine - pitch leads, like in modern electronics, this is a huge plus. The gold layer makes soldering precise and reliable, so you don't have to worry about those annoying solder bridges or cold joints. It's also perfect for wire bonding in high - density integrated circuits. This means your connections will be stable and strong.
2. Superior Protection Against Corrosion
The gold on the surface acts like a superhero shield against oxidation and corrosion. It keeps the copper and nickel layers safe from things like moisture, chemicals, and high heat. So, if you're using your rigid - flex board in tough places - like industrial control systems, automotive electronics, or outdoor communication gear - ENIG is your best bet.
3. Looks Good and Works Well in Assembly
Let's face it, the gold finish makes your board look amazing. In consumer electronics like smartphones and tablets, that matters. But it's not just about looks. The smooth surface makes assembly easier. There's less friction when you're putting in components, which can speed up production.
4. Fits with Different Assembly Ways
Whether you're using reflow soldering, wave soldering, or even manual soldering, ENIG has you covered. This flexibility is a big deal, especially for complex circuit boards with all kinds of components. It also plays nice with automated assembly lines, making your production process more efficient.
1. Nickel Layer Thickness - Get it Right!
The Problem: If the nickel layer is too thin, it's like leaving your copper substrate unprotected. Copper can start to move around and oxidize over time, and that's bad news. But if it's too thick, the gold layer can get stressed during temperature changes. This can lead to cracks or the layers coming apart.
The Impact: Your board's reliability goes down the drain. You might have soldering problems, higher electrical resistance, or even short circuits.
What to Do: Figure out the right nickel layer thickness for your needs. For most boards, there's a common range (around 3 - 5 μm), but if your board will be in a special environment, like high - temperature or high - humidity, you might need to do more tests to get it just right.
2. Control the Immersion Gold Process
The Problem: The temperature, time, and gold concentration during immersion gold are super important. If the temperature's off, you can end up with too much or too little gold. And if the immersion time is wrong, you might get a non - uniform gold layer or the gold might not stick well to the nickel.
The Impact: Non - uniform gold means soldering can be hit - or - miss across the board. And if the gold peels off during assembly or use, you're looking at electrical failures.
What to Do: Use good equipment to keep the process parameters in check. Do regular tests during production. Looking at samples under a microscope to check how the gold is laying down can help you keep things on track.
3. Don't Skip Cleaning and Pretreatment
The Problem: Before ENIG, your board's surface has to be clean. Any oil, oxide, or residue on the copper can stop the nickel and gold from sticking properly. And after ENIG, if you don't clean off the chemical leftovers, they can mess with your board's performance later.
The Impact: Layers that don't stick well can come apart, and chemical residues can corrode the board or make soldering a nightmare.
What to Do: Have a solid pretreatment process that includes cleaning and etching the copper surface. After ENIG, make sure to use the right cleaners to get rid of any residue. In a cleanroom, you can get better control over these steps.
4. Think About Compatibility
The Problem: You need to make sure ENIG works with the components and other materials on your board. Some components are picky about the board's surface finish. High - frequency components or certain sensors, for example, can be sensitive to how the surface treatment affects electromagnetic properties. And if your board touches other materials during assembly or use, there could be chemical reactions or mechanical stress.
The Impact: You could end up with components that don't work right, signal interference, or mechanical failures in your final product.
What to Do: Talk to the component makers to know what they need. Test how ENIG works with other materials your board will be with. If your board goes in a plastic housing, for instance, check for any chemical reactions between the ENIG and the plastic.
1. Smartphone Motherboard Success
We used ENIG for a smartphone motherboard project. The goal was to make sure we could solder all those tiny, high - density components perfectly. We optimized the nickel layer thickness for great protection and adhesion. The immersion gold process was spot - on, giving us a smooth and uniform gold surface. Our cleaning and pretreatment were strict, and it paid off. The motherboard was a breeze to assemble, and the phone works great thanks to the reliable connections ENIG provided.
2. Automotive Electronics Win
For an automotive electronics control unit, ENIG was a must because of the tough environment. The nickel layer was designed to handle temperature changes and chemical exposure in the car. The immersion gold was carefully controlled for long - term stability. Our cleaning and pretreatment steps were thorough to keep contaminants away. And it worked! The ENIG - treated board is doing its job well in the control unit, even with all the challenges of the automotive environment.
We hope this information helps you make the best decisions for your rigid - flex board projects. At
Shenzhen Huaruixin Electronics Co., Ltd., we're always here to help. If you have any questions, feel free to reach out.