Determining the Number of Layers in FPC and Key Considerations in Design
- Nov 07,2024
-
Share
In the field of circuit design, the determination of the number of layers in a Flexible Printed Circuit (FPC) is a crucial decision that impacts the performance, cost, and manufacturability of the final product. Shenzhen Huaruixin Electronics Co., Ltd. is a professional company specialized in the design, production, and sales of FPCs, and has extensive experience and expertise in this regard.
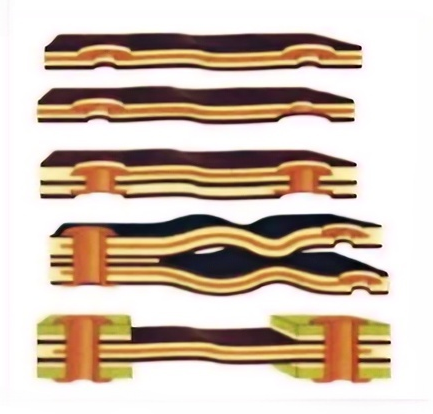
Factors Influencing the Number of FPC Layers
Circuit Complexity
High-density Wiring Requirements: For circuits with a large number of components and complex interconnections, a single-layer or double-layer FPC may not provide sufficient wiring space. In such cases, a multilayer FPC is needed to accommodate the numerous signal traces. For example, in high-performance electronic devices like smartphones and tablets, where components are densely packed, multilayer FPCs are commonly used to ensure the efficient routing of signals.
Signal Separation and Isolation: Some circuits require strict signal separation and isolation to avoid interference between different signals. By using multiple layers, we can allocate specific layers for different types of signals, such as power signals, ground signals, and high-frequency signals. This helps to improve the signal integrity and reduce crosstalk, which is essential for high-speed digital and RF circuits.
Electrical Performance Requirements
Impedance Control: Maintaining a stable and accurate impedance is crucial for the proper functioning of many electronic circuits, especially for high-frequency and high-speed signals. The number of layers in an FPC can affect the impedance characteristics of the circuit. By carefully designing the layer structure and the thickness of the dielectric layers, we can achieve the desired impedance values. For example, adding more ground and power planes can help to control the impedance and improve the signal quality.
Power Distribution: In circuits with high power consumption, a sufficient number of power planes are needed to ensure the stable supply of power. Multilayer FPCs can provide dedicated power layers, which can reduce the resistance and voltage drop in the power distribution network, improving the power efficiency and reliability of the circuit.
Space Constraints
Limited Board Area: In some applications where the available space for the circuit board is limited, a multilayer FPC can be a solution to maximize the wiring density within a small area. By stacking the layers, we can fit more circuits into a smaller space, which is particularly important for wearable devices, medical instruments, and other compact electronic products.
Three-dimensional Layout: For circuits that need to be arranged in a three-dimensional space, such as in some flexible display or foldable device applications, a multilayer FPC can provide the flexibility to conform to the complex geometry and enable the realization of the desired circuit layout.
Cost and Manufacturing Constraints
Manufacturing Cost: Generally, the manufacturing cost of a multilayer FPC is higher than that of a single-layer or double-layer FPC due to the increased complexity of the manufacturing process. The cost factors include the cost of materials, the number of manufacturing steps, and the requirement for advanced manufacturing equipment and technology. Therefore, we need to balance the performance requirements and the cost constraints when determining the number of layers.
Manufacturing Feasibility: The manufacturing process of an FPC also imposes certain limitations on the number of layers. For example, the thickness of the FPC, the alignment accuracy between layers, and the via hole manufacturing technology all affect the feasibility of manufacturing a multilayer FPC. We need to ensure that the designed FPC can be manufactured reliably and with high quality.
Key Considerations in FPC Design
Layer Stackup Design
Symmetry and Balance: To ensure the mechanical stability and flatness of the FPC, the layer stackup should be designed to be symmetrical. This means that the number of layers on each side of the central plane should be equal, and the thickness and material properties of the layers should be as similar as possible. For example, if there are two signal layers on one side of the central plane, there should be two corresponding signal layers on the other side.
Coupling between Layers: The coupling between the signal layers and the reference planes (such as the power and ground planes) is important for signal integrity. We should minimize the distance between the signal layers and the reference planes to enhance the coupling effect and reduce the electromagnetic interference. At the same time, proper use of dielectric materials with suitable thickness and dielectric constant can also improve the coupling performance.
Via Design
Via Size and Placement: The size and placement of the vias need to be carefully designed to ensure the electrical connection between the layers while minimizing the impact on the signal integrity. The via diameter should be as small as possible to reduce the occupation of the wiring space, but it also needs to meet the requirements of the manufacturing process and the current-carrying capacity. The placement of the vias should avoid interfering with the signal traces and components, and ensure a reasonable distribution of the vias to ensure the uniformity of the current and signal distribution.
Via Stub Minimization: Via stubs are the unused portions of the vias that remain after the connection is made between the layers. These stubs can cause signal reflection and crosstalk, affecting the signal quality. Therefore, in the design process, we should try to minimize the length of the via stubs by using appropriate via drilling techniques and layer stackup designs.
Signal Routing
Routing Rules: When routing the signals on the FPC, we need to follow the relevant routing rules and design guidelines to ensure the correctness and reliability of the signal transmission. For example, the signal traces should avoid sharp turns and corners, and use smooth curves as much as possible to reduce the signal reflection and attenuation. The width and spacing of the signal traces should be designed according to the current-carrying capacity and the impedance requirements.
Cross-layer Routing: In multilayer FPCs, cross-layer routing is inevitable. When routing signals across different layers, we need to ensure that the return current can flow smoothly from one layer to another. This requires proper design of the reference planes and the via connections to provide a low-impedance return path for the signals.
In conclusion, the determination of the number of layers in an FPC is a complex decision that needs to consider various factors such as circuit complexity, electrical performance requirements, space constraints, and cost. By carefully considering these factors and following the key design considerations, we can design an FPC that meets the requirements of the application and has excellent performance. Shenzhen Huaruixin Electronics Co., Ltd. has a professional design and manufacturing team that can provide high-quality FPC products and solutions to meet the diverse needs of customers.