Decoding the Intricate Blueprint of Drone FPC Production: A Holistic Expedition
- Jan 07,2025
-
Share
Hey there, drone enthusiasts and tech connoisseurs! In the dynamic and perpetually advancing realm of drones, Flexible Printed Circuits (FPCs) stand as the unsung heroes, underpinning their very functionality. As a vanguard in the drone FPC arena, Shenzhen Huaruixin Electronics Co., Ltd. has amassed a trove of profound knowledge and hands-on expertise. Today, let's embark on an in-depth exploration of the minute particulars that command our unwavering attention throughout the entire FPC production odyssey for drones, traversing from the drawing board of design to the safeguarding embrace of packaging.
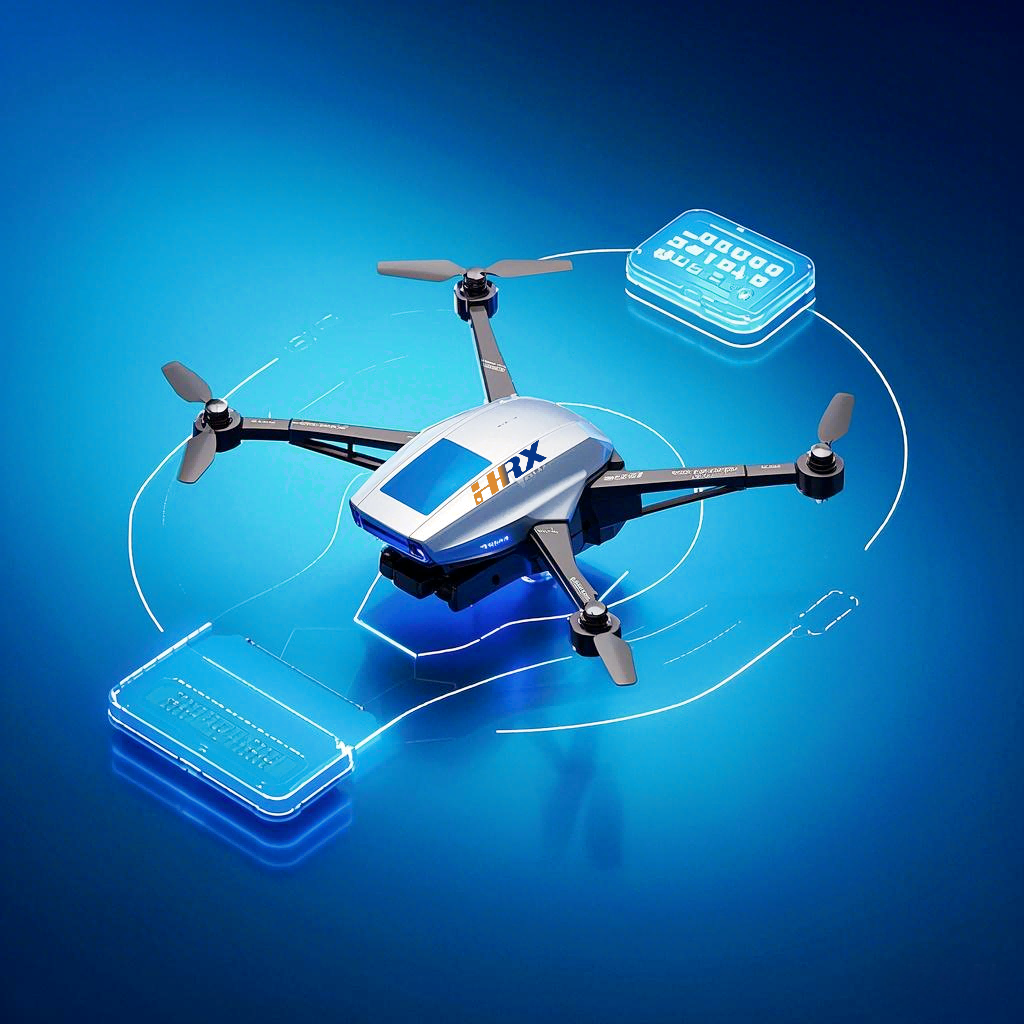
1. Design Stage: Forging the Foundation of Excellence
A.Miniaturization and Layout Optimization: Drones epitomize the zenith of compact engineering, and FPCs must contort and nestle themselves into their constricted interiors. When architecting an FPC for a consumer-grade selfie drone, our virtuoso team at Shenzhen Huaruixin Electronics Co., Ltd. had to summon their creative prowess. Leveraging cutting-edge computer-aided design (CAD) software fortified with advanced layout algorithms, we painstakingly choreographed the circuitry layout. By artfully folding and meticulously routing the FPC, we achieved an optimal space utilization paradigm. This allowed us to seamlessly integrate all essential components, such as the camera interface connectors, flight control signal pathways, and the intricate web of battery management circuitry, onto a singular, ultra-compact FPC. Not only did this parsimonious design conserve precious spatial real estate, but it also curtailed the overall heft of the drone, supercharging its flight performance and endurance.
B.Signal Integrity and Impedance Matching: In the high-stakes world of drones, especially those deployed for professional aerial photography or geospatial surveying, high-velocity data transmission is the lifeblood. In a project centering around a high-resolution mapping drone, our engineers dedicated themselves to the pursuit of impeccable impedance control. The differential pairs, those conduits of data shuttling between the imaging sensor and the onboard storage unit, were sculpted with surgical precision. By finessing the trace widths, spacing intervals, and handpicking dielectric materials with calibrated permittivity, we achieved impedance matching within a razor-thin tolerance of ±3 ohms. This herculean feat ensured error-free, lightning-fast data transfer, empowering the drone to capture and archive exquisitely detailed images without a single pixel of data loss.
C.Mechanical Considerations: Drones are subjected to a ceaseless barrage of vibrations and dynamic movements during their airborne sojourns. When devising an FPC for a racing drone, we incorporated flexible yet stalwart materials. By interlacing a slender layer of aramid fiber reinforcement in stress-prone zones, such as the vicinities of motor connectors and gimbal mounts, we bolstered the FPC's mechanical fortitude. This preemptive measure staved off trace fractures and guaranteed unfaltering power and signal conveyance, even when the drone was executing the most audacious aerial acrobatics.
2. Production Process: Transforming Designs into Tangible Reality
A.Material Selection and Handling: The choice of substrate and conductive materials is the cornerstone of FPC quality. For a long-range delivery drone braving diverse meteorological conditions, we zeroed in on a high-performance polyimide (PI) substrate with a thickness of 35 micrometers. Renowned for its exceptional heat resistance and pliability, it empowered the FPC to weather temperature oscillations and mechanical duress. The copper foil, the workhorse of conductivity, was meticulously chosen too. In regions responsible for power distribution, a 50-micrometer-thick copper foil was deployed to minimize resistance and optimize current flow. Meanwhile, for the labyrinthine signal routing, a 25-micrometer-thick foil enabled the etching of finer, more intricate traces, facilitating complex circuit designs.
B.Precision Manufacturing Techniques: Micro-vias and blind vias are the clandestine passageways that breathe life into multi-layer FPCs. In the production of an FPC for a military-grade surveillance drone, our state-of-the-art laser drilling apparatus, calibrated to micron-level precision, was summoned to bore micro-vias with diameters as diminutive as 80 micrometers. These micro-vias were then plated with a proprietary electroplating process, ensuring seamless electrical connectivity between layers. The etching phase was equally pivotal. By stringently governing the etching parameters, such as the concentration of the etching solution, temperature gradients, and time intervals, we achieved trace widths with a tolerance of ±5 micrometers, satisfying the exacting demands of the drone's circuitry.
C.Environmental Control: Maintaining a pristine and meticulously controlled production milieu is non-negotiable. Our production facility dedicated to drone FPCs is outfitted with HEPA filters, acting as sentinels against particulate intrusion, ensuring a dust-free haven. Temperature and humidity levels are regimented at 22°C ± 2°C and 45% - 55% respectively. This stable microclimate thwarts issues like moisture ingress, which could compromise the FPC's electrical performance, and dust contamination, a potential harbinger of short circuits.
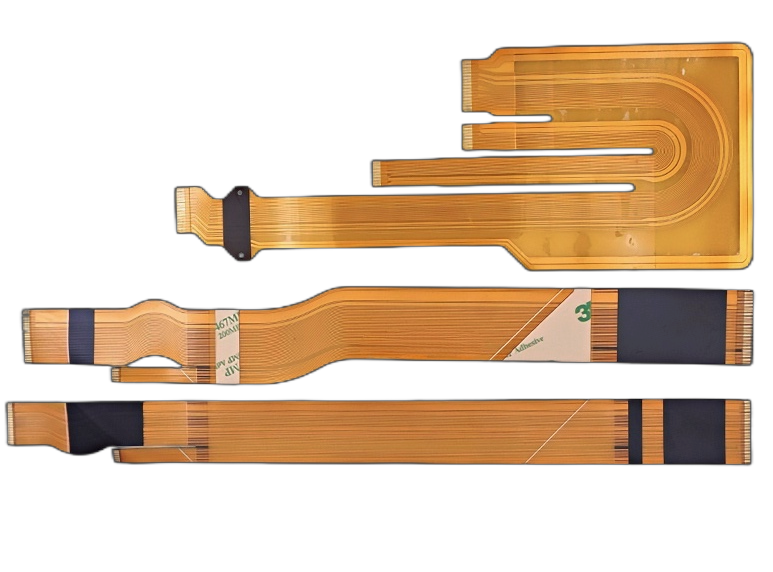
3. Quality Inspection: Guaranteeing Impeccable Performance
A.Visual Inspection: At each milestone of the production process, our seasoned technicians conduct visual audits. In the case of a widely coveted consumer drone FPC, any aberration, be it a scratch, dent, or discoloration on the surface, is promptly flagged. The solder joints, those microscopic junctions of connectivity, are scrutinized under high-powered magnification to ascertain proper wetting and the absence of cold soldering. Given that even the most minuscule defect can precipitate a catastrophic failure in the drone's operation, our vigilance knows no bounds.
B.Electrical Testing: Comprehensive electrical assays are the norm. For an FPC earmarked for a scientific research drone, we execute open-circuit and short-circuit diagnostics to confirm the integrity of all connections. Impedance spectroscopy, a powerful analytical tool, is employed to validate impedance values across a spectrum of frequencies, ensuring reliable signal propagation. Additionally, insulation resistance tests are carried out to fortify the integrity of the insulating layers, barricading against any leakage currents that could wreak havoc on the drone's components.
C.Reliability Testing: To mimic the rigors of the real world, we subject FPCs to a gauntlet of reliability tests. In the development of an FPC for an agricultural spraying drone, it endured thermal shock trials, cycling between -20°C and +60°C to mirror the temperature extremes in the field. Humidity tests at 95% relative humidity for protracted durations were also administered to gauge moisture resistance. Vibration tests, calibrated to resonate with the frequencies and amplitudes the drone experiences during flight, ascertained the FPC's mettle against mechanical stress, ensuring it emerged unscathed.
4. Packaging: Shielding the Crown Jewel
A.Anti-static and Moisture-proof Packaging: Drone FPCs are hypersensitive to electrostatic discharge (ESD) and the insidious encroachment of moisture. For all our FPC shipments, we employ anti-static bags crafted from static-dissipative polymers. These bags act as a prophylactic shield, neutralizing any static buildup that could zap the delicate circuitry. Desiccants, those silent moisture absorbers, are also incorporated to wick away any errant humidity, safeguarding the FPC from corrosion induced by dampness. For instance, in the packaging of FPCs for a high-altitude weather monitoring drone, this added layer of protection ensured the FPCs arrived in mint condition, primed for assembly.
B.Shock and Vibration Protection: During transit, FPCs must be cocooned from impacts. We deploy custom-engineered foam inserts and corrugated cardboard boxes, a dynamic duo. The foam, with its cushioning prowess, absorbs shocks, while the robust box provides structural integrity. When shipping FPCs for a professional cinematography drone, this packaging symbiosis safeguarded the FPCs from the travails of transportation, preventing any damage that could mar their functionality.
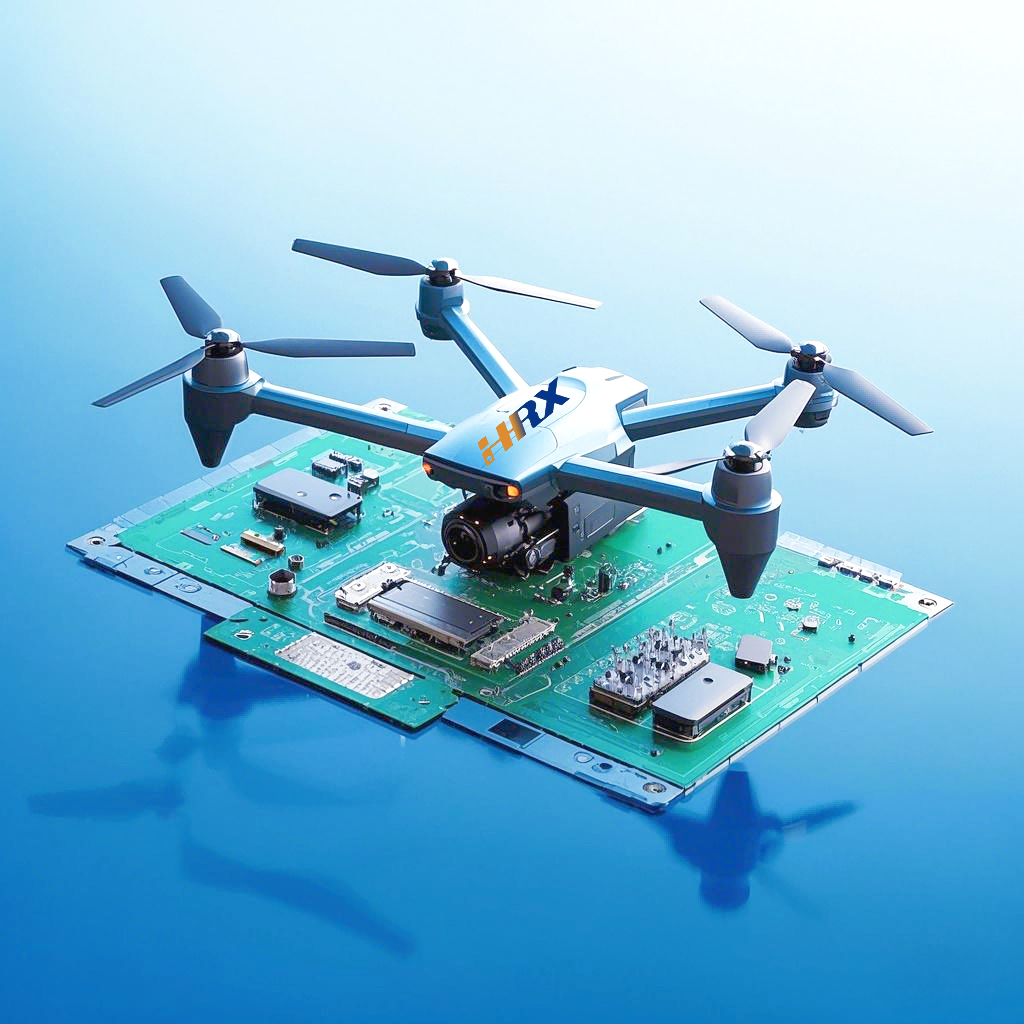
In conclusion, crafting top-tier FPCs for drones is a complex, yet immensely gratifying endeavor. At Shenzhen Huaruixin Electronics Co., Ltd., we've honed our processes over the years through relentless innovation and a commitment to quality. Whether you're a drone manufacturer seeking to supercharge your FPC supply chain or a curious mind eager to unravel the technological tapestry behind drones, we wholeheartedly welcome you to join the discourse. Let's ascend to new pinnacles in drone technology together!
So, what are your thoughts? Have you encountered any challenges with drone FPCs? Share your experiences in the comments below. Until next time, happy flying and designing!