Decoding the Enigmatic Blueprint of FPC Design, Production, and Delivery for Customized Medical Aesthetics and Physiotherapy Treasures
- Dec 04,2024
-
Share
In the dynamic and progressive landscape of medical technology, the clamor for bespoke FPC (Flexible Printed Circuit) in the realm of physiotherapy and aesthetic medical products is reaching new crescendos. Shenzhen Huaruixin Electronics Co., Ltd., armed with a profound reservoir of proficiency in FPC manufacturing and vending, holds the key to unlocking the Pandora's box of vital elements that warrant meticulous attention during the odyssey of design, production, and delivery of these circuits.
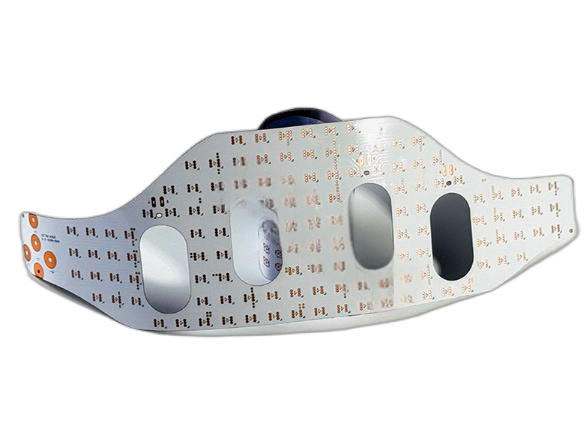
1. Design Phase
Functionality and Compatibility: The Symbiotic Bond
The FPC blueprint must be meticulously sculpted to dovetail with the idiosyncratic functions of the physiotherapy or aesthetic medical contraption. It must coalesce harmoniously with ancillary components such as sensors, electrodes, and microcontrollers. Take, for instance, in the FPC of a laser beauty apparatus, the circuitry is tasked with the solemn duty of ensuring a seamless and stable power supply and unerring signal transmission for the laser emitter and its governing control system. Any misalignment in the design schematic can precipitate a catastrophic malfunction or a lackluster performance of the entire device, rendering it ineffective or even hazardous.
Safety and Reliability: The Twin Pillars of Trust
Given the sacrosanct medical nature of these products, safety reigns supreme. The FPC layout ought to be imbued with astute insulation and grounding stratagems to stave off the specter of electrical leakage and the perils of shock. Redundant circuits or fail-safe architectures can be artfully woven into the design fabric to supercharge reliability. Consider a physiotherapy device that harnesses electrical stimulation; here, the FPC should be fortified with backup conduits to guarantee uninterrupted operation even in the face of a partial circuit meltdown, thereby safeguarding the patient from any potential harm.
Miniaturization and Flexibility: The Art of Compact Conformance
To snugly nestle within the snug and often ergonomically crafted chassis of medical devices, the FPC must be a paragon of miniaturization without compromising an iota of performance. The supple essence of FPC empowers it to contort and adapt to a myriad of shapes and curvatures, a boon for wearable or handheld medical gizmos. However, this mandates a painstaking deliberation of trace widths, via dimensions, and layer stack-ups to safeguard signal integrity and mechanical tenacity.
2. Production Phase
Material Selection: The Alchemy of Choice
The selection of materials is nothing short of a high-stakes gamble. Biocompatible substances must be the cornerstone to ensure that the FPC remains innocuous when in intimate contact with the human corporeal form. Materials with high-temperature resistance and chemical stability are also non-negotiable, as certain medical devices may be subjected to sterilization regimens or exposed to a cauldron of chemicals. Picture a skin rejuvenation device that deploys chemical gels; the FPC must be impervious to the corrosive onslaught of these gels, emerging unscathed and fully functional.
Manufacturing Process Precision: The Quest for Perfection
The production pilgrimage demands a zenith of precision. Fine-pitch component soldering, pinpoint etching, and exacting lamination are the trifecta of essentiality. Any infinitesimal deviation in these processes can spawn open circuits, short circuits, or the bane of delamination. State-of-the-art manufacturing apparati and draconian process control are the sine qua non for ensuring a uniform and sterling quality output. For example, the etching sojourn must be monitored with a hawk's eye to actualize the precise trace widths and clearances as ordained by the design, and the solding temperature and temporal parameters must be finessed to forge reliable connections for the diminutive components.
Quality Testing: The Rigorous Inquisition
Stringent quality testing is the litmus test of excellence. Beyond the quotidian electrical assays like continuity and impedance testing, bespoke tests for medical applications such as dielectric strength evaluation and biocompatibility verification must be unfailingly carried out. Any defective FPCs must be unearthed and banished before they infiltrate the hallowed halls of medical devices. Consider dielectric strength testing, which certifies that the FPC can weather the requisite voltages without capitulating to breakdown, a linchpin for the safety of both the medical device and the patient it serves.
3. Delivery Phase
Packaging and Protection: The Coccoon of Care
The FPCs necessitate a packaging regimen that cocoons them from the ravages of physical damage, the insidious encroachment of moisture, and the lurking threat of electrostatic discharge during the peregrinations of transportation and storage. Anti-static pouches and shock-absorbing packaging accoutrements are the weapons of choice. Envision the shipping of FPCs for a portable ultrasound device; proper packaging serves as a bulwark, shielding the delicate circuitry from the vagaries of rough handling during transit.
Documentation and Traceability: The Chronicle of Accountability
Meticulous documentation is the lodestar. Each FPC should bear a unique insignia and be accompanied by a detailed dossier of production chronicles, spanning material provenance, manufacturing processes, and test outcomes. This bequeaths effortless traceability in the event of any quality conundrums or the dreaded recall. For instance, if a snag is unearthed in a particular batch of FPCs utilized in a medical device, the documentation acts as a trusty compass, swiftly pinpointing the root cause and the afflicted products, thereby streamlining the corrective measures.
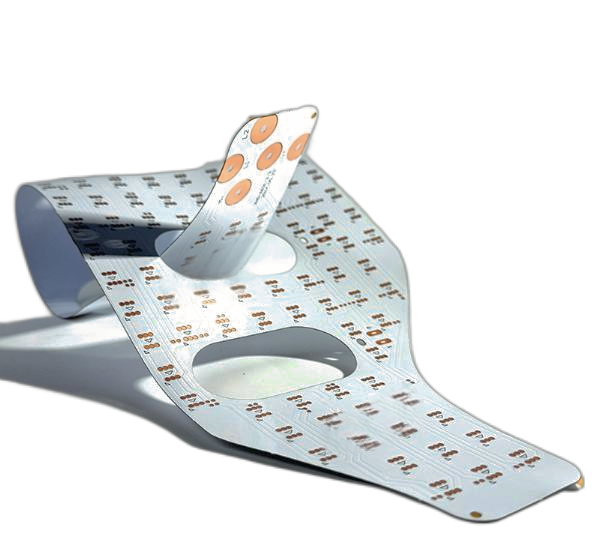
In summation, the design, production, and delivery of FPC for customized physiotherapy and aesthetic medical products is a veritable labyrinth of technical and quality-centric considerations.
Shenzhen Huaruixin Electronics Co., Ltd. stands poised and primed to surmount these challenges and is eager to engage in a collaborative dance with customers to conjure up top-tier FPC solutions for the burgeoning medical technology industry.