In the domain of manufacturing LED flexible light strip boards and custom FPC cable soft light boards, the choice of materials is an elemental determinant of product quality and performance. Herein, we dissect some of the cardinal issues and offer sagacious suggestions.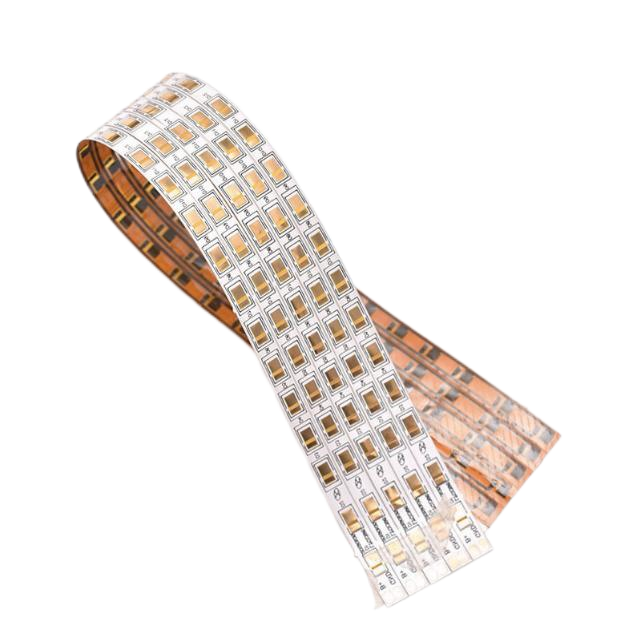
1. FPC Substrate Material: The Foundation of Flexibility and Durability
The substrate of FPC, predominantly polyimide (PI), presents a multifaceted set of characteristics that demand meticulous attention. PI is lauded for its extraordinary heat resistance, which endows LED light strip boards with the capacity to function stably even under elevated temperature conditions, such as in industrial high-intensity lighting applications where continuous heat dissipation is a concern. Its flexibility is another hallmark, allowing for the boards to be contorted and installed in diverse and often confined spaces. For instance, in wearable technology lighting components, where the light strip must adapt to the body's contours, a thinner PI substrate, typically ranging from 0.05mm to 0.1mm, is the material of choice due to its enhanced pliability. Conversely, in scenarios like large-scale indoor decorative light installations or industrial fixtures that necessitate a certain degree of structural rigidity, a thicker PI substrate, within the 0.1mm - 0.2mm spectrum, is more aptly suited.
The copper foil, an integral conductive element within the FPC, is equally critical. Its thickness and quality are directly proportional to the electrical conductivity and overall efficacy of the light strip board. In low-power LED flexible light strip applications, a 18μm copper foil suffices to ferry the requisite electrical current. However, in high-power exigencies, such as in the realm of outdoor advertising signage where luminosity and consistency are of the essence, a 35μm or thicker copper foil is mandated. This not only mitigates resistance-induced heat generation but also ensures a seamless flow of electricity. Paramount to the success of the FPC is the adhesion between the copper foil and the PI substrate. In automotive interior lighting systems, where vibrations and temperature fluctuations are commonplace, a robust adhesive bond between the copper foil and substrate is non-negotiable. Any detachment could precipitate electrical failures and compromise the safety and functionality of the lighting apparatus.
2. LED Chips: Illuminating the Path to Optimal Performance
The selection of LED chips is a nuanced process that hinges on multiple variables. The luminous efficiency and wavelength of the chips are the primary considerations. In the context of indoor illumination, white LED chips with a high luminous efficiency and a color temperature spanning 2700K - 6500K are essential for creating a conducive and comfortable lighting ambience. In hospitality settings like hotel rooms, a color temperature of around 3000K imparts a warm and inviting glow, while in office spaces, a 5050K neutral white is favored for its ability to enhance visual acuity and productivity. For color-centric LED light strips, such as those deployed in the realm of stage lighting and artistic installations, pinpoint accuracy in wavelength control is the sine qua non for achieving a vivid and accurate chromatic display.
The physical dimensions and packaging of LED chips also wield a significant influence. Smaller form-factor chips, such as those in 0201 and 0402 packages, are the darlings of applications where space is at a premium and precision is paramount. Mobile device peripherals, like the decorative light strips adorning the bezels of smartphones, exemplify the utility of such diminutive chips, which can be densely arrayed to produce a seamless and refined luminous effect. Larger chips, like the 3528 and 5050 packages, are the go-to for scenarios demanding high luminous flux. Commercial storefront signage and outdoor lighting fixtures rely on these chips to project a bright and far-reaching illumination. The Surface Mount Device (SMD) packaging format has emerged as the industry standard, owing to its compactness, uniform light dispersion, and amenability to automated manufacturing processes. A case in point is the smart bracelet industry, where 0201 SMD packaged LED chips have revolutionized the way wearable devices incorporate lighting features, offering a harmonious blend of aesthetics and energy efficiency.
3. Cover Layer Materials: Protecting and Perfecting the Product
The protective film, a key constituent of the cover layer, must possess a trifecta of properties: abrasion resistance, chemical corrosion resistance, and optical transparency. In outdoor LED light strip applications, such as those adorning street lamps and building facades, the protective film is the first line of defense against the elements. A film with superior UV resistance is indispensable, as it staves off the deleterious effects of prolonged sun exposure, including yellowing and loss of transparency. Additionally, the film's hardness must strike a delicate balance. It should be robust enough to fend off superficial scratches and abrasions during installation and operation, yet pliable enough to withstand the rigors of bending and flexing without cracking. An illustrative example is an urban landscape lighting project, where the LED flexible light strips were sheathed in a PET protective film. After years of exposure to the vagaries of weather, the film maintained its optical clarity and protective integrity, thereby safeguarding the luminosity and longevity of the light strips.
The solder mask, another vital component of the cover layer, serves a dual purpose. It acts as a shield, preventing solder from bridging unintended electrical connections during the soldering process. Its color, typically a dark hue such as green or black, is not a matter of aesthetics alone. A darker color facilitates visual inspection and precise alignment during the manufacturing process, especially in complex circuit board designs. In industrial automation equipment, where LED light strips are used for status indication and signaling, a black solder mask not only averts short circuits but also streamlines the assembly process, leading to enhanced production efficiency and product reliability.
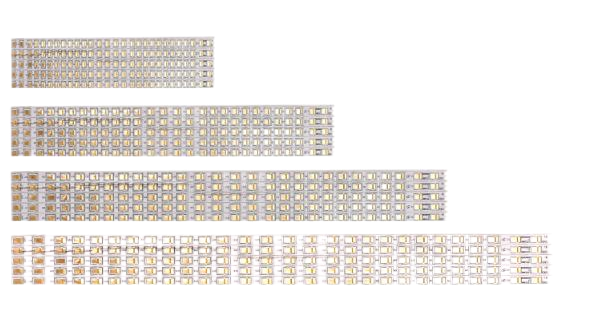
Shenzhen Huaruixin Electronics Co., Ltd., a paragon in the FPC manufacturing industry, has amassed a wealth of experience in material selection. In a recent project for a sprawling shopping mall, the company's expertise was on full display. By astutely selecting a PI substrate with optimal heat resistance and flexibility, coupling it with a precisely calibrated copper foil thickness, and integrating high-quality LED chips with impeccable color rendering and luminous efficiency, the company crafted LED flexible light strip boards that not only met but exceeded the mall's exacting lighting requirements. Complemented by a top-tier cover layer comprising a durable protective film and a reliable solder mask, the light strip boards have withstood the test of time and the rigors of a bustling commercial environment, earning plaudits from the client. The company remains steadfast in its commitment to excellence and extends an open invitation to both new and existing clients to engage in a collaborative dialogue, with the shared objective of pioneering novel and superior LED flexible light strip board and FPC cable soft light board solutions.