A Comprehensive Guide to EMC Issues in the Design and Production of FPCs for Home Appliances
- Dec 24,2024
-
Share
I. Introduction
In the highly competitive panorama of home appliance manufacturing, electromagnetic compatibility (EMC) of Flexible Printed Circuits (FPCs) stands as an uncompromisable requisite. EMC stipulates that an FPC must neither emit excessive electromagnetic interference (EMI), which could perturb other adjacent electronic apparatuses, nor exhibit undue susceptibility to external EMI that might instigate malfunctions in the associated home appliance. Shenzhen Huaruixin Electronics Co., Ltd., a preeminent luminary in FPC production and sales, proffers this elaborate guide to assist manufacturers in traversing the labyrinthine domain of EMC within home appliance FPCs.
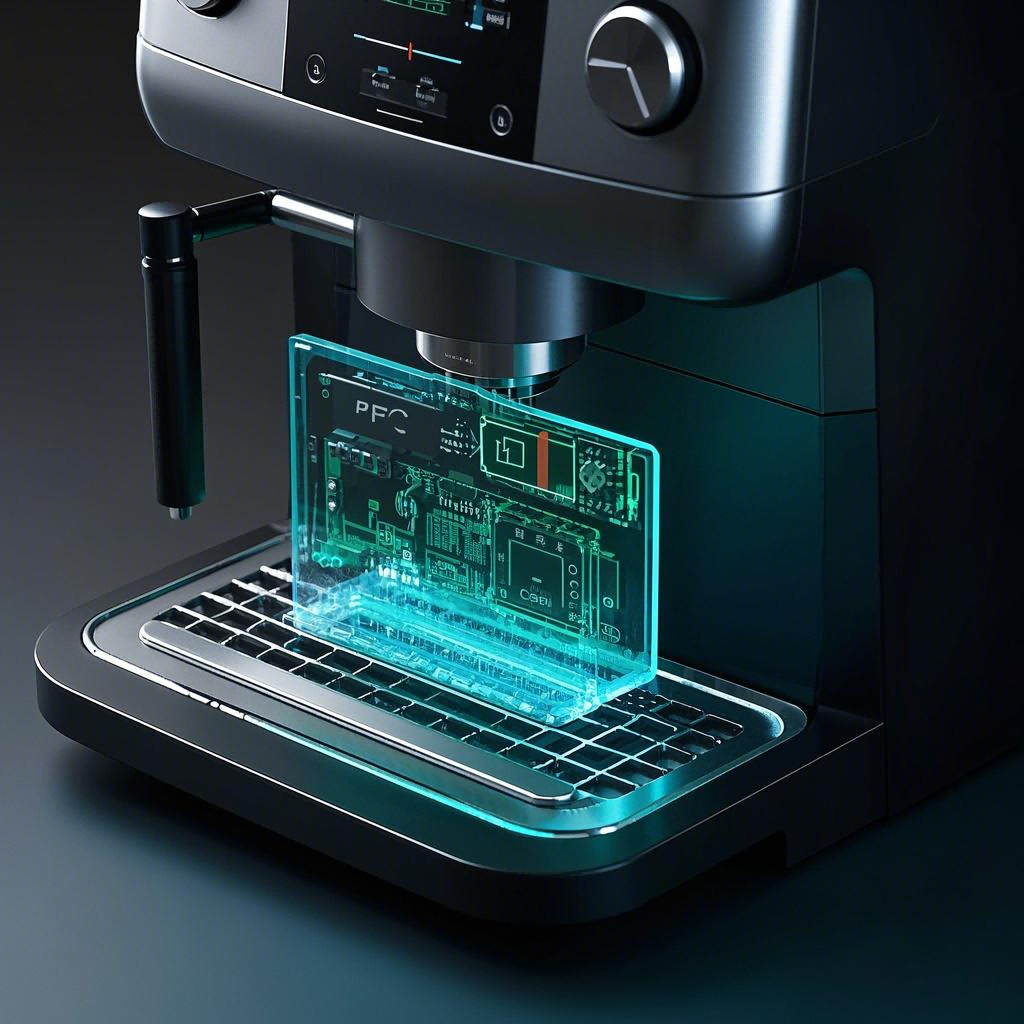
II. EMI Emission Control
A. High-Frequency Noise Source Identification
Switching Power Supplies: These are renowned as prolific EMI progenitors in home appliances. The rapid toggling of transistors within power supply circuits begets high-frequency harmonics. To allay this, the employment of soft-switching modalities such as zero-voltage switching (ZVS) or zero-current switching (ZCS) can be contemplated. Additionally, snubber circuits, constituted by resistors, capacitors, and sporadically diodes, can be appended across the switching elements to attenuate the voltage and current spikes that contribute to EMI. The snubber circuit functions by absorbing the energy stored in the parasitic inductance and capacitance of the switching components, thereby mollifying the rate of change of voltage and current.
Clock Signals and High-Speed Data Lines: Microcontrollers and other digital constituents in home appliances frequently possess clock signals and high-speed data buses. These can radiate EMI if not adroitly engineered. The utilization of differential signaling for high-speed data conveyance, with a meticulously regulated impedance of the differential pairs, can curtail EMI. Shielding the clock lines and data buses with a grounded conductive stratum, like a copper shield, can also prove efficacious. Differential signaling, wherein two complementary signals are transmitted, mitigates the impact of common-mode noise as the noise tends to affect both signals identically and can be cancelled out at the receiver.
B. Filtering and Suppression Strategies
Capacitor Selection and Placement: Decoupling capacitors are of primordial importance. For instance, ceramic capacitors with low equivalent series inductance (ESL) and equivalent series resistance (ESR) should be positioned as proximate as feasible to the power pins of integrated circuits. Their raison d'être is to furnish a local reservoir of charge, diminishing the voltage vacillations that can precipitate EMI. Bulk capacitors, such as electrolytic capacitors, can be deployed to handle more substantial energy storage exigencies and filter out lower-frequency din. The ESL and ESR of a capacitor determine its ability to respond rapidly to changes in voltage and current, with lower values being preferable for high-frequency noise suppression.
Ferrite Beads and Chokes: Ferrite beads are efficacious in attenuating high-frequency noise. They can be interposed in series with power lines or signal lines. Common-mode chokes, which feature two windings coiled around a solitary ferrite core, are employed to quell common-mode noise. For example, in a washing machine FPC that interconnects the control board and the motor driver, a common-mode choke can be installed in the power cable to preclude common-mode noise from the motor from proliferating back to the control board. A ferrite bead exploits the magnetic properties of the ferrite material to impede the flow of high-frequency currents, while a common-mode choke capitalizes on the differential coupling of the windings to suppress common-mode noise.
C. Grounding and Shielding Techniques
Ground Plane Design: A continuous and low-impedance ground plane is cardinal. It should be contrived to minimize ground loops, which can metamorphose into antennas for EMI. Partitioning the ground plane into discrete sections for analog and digital circuits and interconnecting them at a singular point (single-point grounding) or employing a hybrid of single-point and multi-point grounding contingent on the signal frequencies can assist in reducing EMI coupling. A ground plane serves as a reference potential and a conduit for the return current of signals, and proper partitioning and grounding strategies are essential to avert the formation of ground loops that can introduce noise.
Shielding Implementation: For FPCs in appliances like microwave ovens or televisions, where EMI emission can be substantial, shielding is imperative. A conductive shielding lamina, such as a copper foil or a metalized polyester film, can be laminated onto the FPC. The shielding layer must be aptly grounded to be efficacious. Moreover, encasing the FPC in a metal housing or employing shielded connectors can further augment the shielding effect. The shielding layer functions by reflecting and absorbing electromagnetic waves, thereby confining the EMI within the shielded enclosure or precluding external EMI from infiltrating.
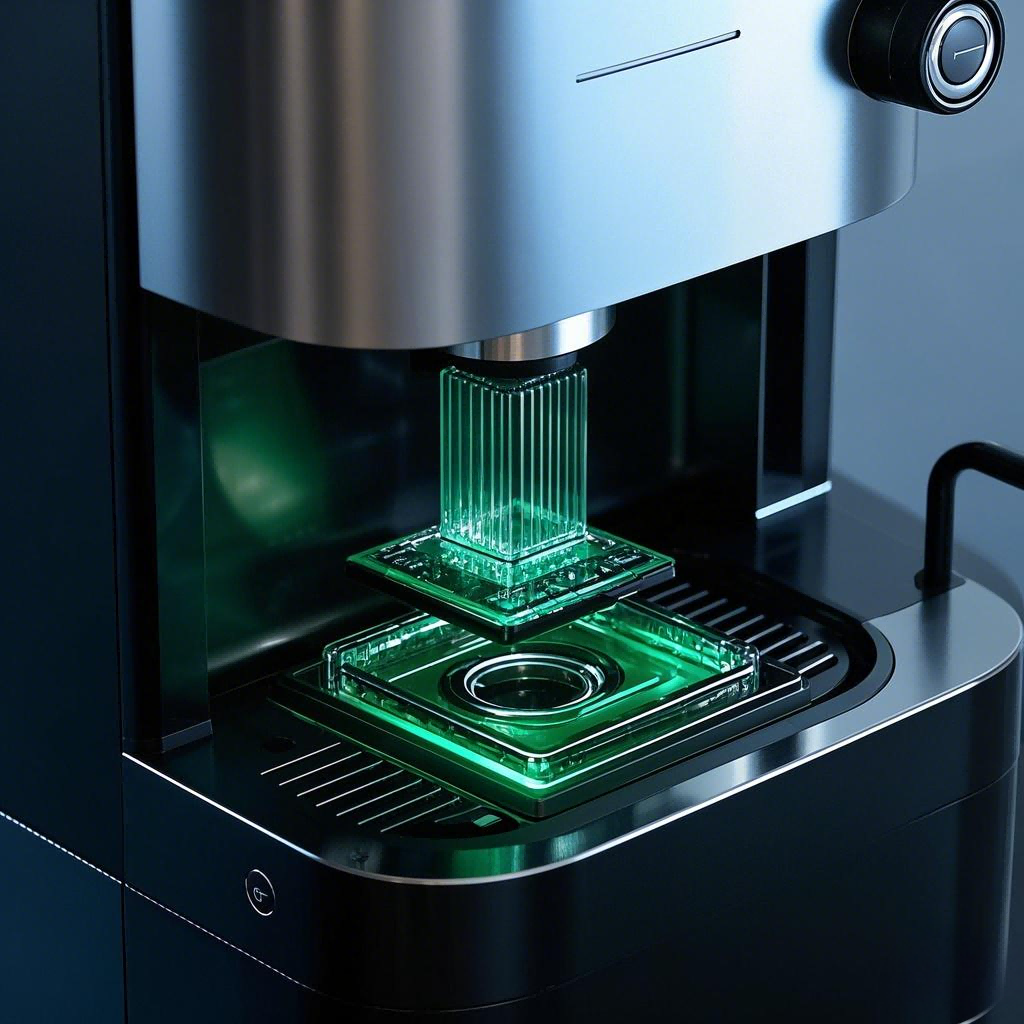
III. Susceptibility to External EMI Reduction
A. External Interference Sources Awareness
Wireless Devices: With the ubiquity of Wi-Fi routers, Bluetooth contrivances, and mobile phones in contemporary domiciles, home appliances are incessantly exposed to their electromagnetic fields. The FPC design ought to factor in the frequency bands of these wireless apparatuses. For example, integrating filters that are attuned to occlude the frequencies of prevalent wireless communication bands can forestall interference. In a smart refrigerator FPC, a band-stop filter can be incorporated to attenuate the 2.4 GHz and 5 GHz Wi-Fi signals that might otherwise couple into the circuit and vitiate the operation of the refrigerator's control system. A band-stop filter is designed to attenuate signals within a specific frequency band, thereby shielding the FPC from unwanted external interference.
Power Line Interference: The power grid can harbor sundry types of interference, including spikes, surges, and harmonic distortion. To safeguard the FPC from power line interference, surge suppressors can be appended at the power input of the appliance. These can be metal oxide varistors (MOVs) or transient voltage suppressor (TVS) diodes, which can clamp the voltage to a secure level during power line surges. MOVs operate by varying their resistance based on the applied voltage, while TVS diodes offer a rapid response and low clamping voltage to protect against transient overvoltages.
B. Filtering and Isolation Measures
Common-Mode and Differential-Mode Filters: In addition to the filters expounded upon earlier for EMI emission control, filters can be harnessed to preclude external interference from infiltrating the FPC. Common-mode filters are engineered to obstruct common-mode noise that manifests on both conductors of a cable or signal line relative to the ground. Differential-mode filters, conversely, target the noise between the two conductors of a differential pair. For example, in a home theater system's FPC, where audio and video signals are transmitted, differential-mode filters can be utilized to vouchsafe the integrity of the signals by expunging any external differential-mode noise. These filters function by presenting different impedances to the common-mode and differential-mode signals, thereby selectively attenuating the unwanted noise components.
Isolation Components: Isolation transformers and optocouplers can be enlisted to provide electrical isolation between disparate segments of the FPC or between the FPC and other components in the appliance. Isolation transformers operate on the principle of magnetic coupling and can preclude the transfer of electrical noise through the transformer windings. Optocouplers employ an optical interface to couple signals between two electrically isolated circuits, thereby severing the path of electrical noise. Isolation transformers ensure galvanic isolation, which is crucial in applications where safety and noise immunity are paramount, while optocouplers offer a fast and reliable means of signal transfer across an isolation barrier.
C. Cable and Connector Considerations
Shielded Cables: Cables interconnecting diverse parts of the appliance and the FPC should be shielded. The shielding of the cable can be a braided copper wire or a foil shield. The shield must be appropriately grounded at both termini to be efficacious. For example, in a vacuum cleaner with a detachable hose and FPC liaison, the cable linking the hose-mounted controls to the main body of the vacuum cleaner should be a shielded cable to preclude external EMI from coupling into the FPC. The shielding of the cable acts as a Faraday cage, impeding the ingress of external electromagnetic fields and containing any internal EMI.
Connector Design: Shielded connectors should be utilized to mate with the shielded cables. The connectors should possess a 360-degree shielding contact to ensure a continuous shield path. Gold-plated contacts can be employed to enhance the electrical conductivity and diminish the contact resistance, which in turn aids in maintaining the integrity of the signal and averting the ingress of EMI. The 360-degree shielding contact guarantees a seamless connection of the cable shield to the connector housing, minimizing the potential for EMI leakage or ingress at the connection point.
IV. Layout and Routing Optimization for EMC
A. Trace Length and Loop Area Minimization
Short Trace Routing: Keeping the traces as abbreviated as possible curtails the inductance and capacitance, thereby diminishing the coupling of electromagnetic fields. In a coffee maker FPC, for instance, the traces interfacing the temperature sensor and the control chip should be routed in the most direct fashion. Employing vias and multilayer routing can facilitate the attainment of shorter trace lengths. Vias are conductive holes that enable the connection between different layers of the FPC, allowing for more efficient routing and shorter trace paths.
Loop Area Reduction: Minimizing the loop area formed by signal and power traces is crucial. This can be effected by routing the traces in a manner such that the return path of the signal is proximate to the signal trace. For example, in a toaster's FPC, the power and ground traces for the heating element should be routed adjacently to curtail the loop area and thus the EMI. A smaller loop area implies a lower magnetic flux, which in turn reduces the potential for EMI generation and susceptibility.
B. Component Placement Strategies
Separation of Sensitive and Noisy Components: Sensitive components such as microcontrollers, sensors, and analog circuits should be positioned at a remove from noisy components like motors, relays, and switching power supplies. In a dishwasher FPC, the microcontroller that governs the washing cycle should be situated at a sufficient distance from the motor driver and the power supply components to avert EMI coupling. This spatial segregation helps to reduce the magnetic and electric field interactions between the components, minimizing the risk of interference.
Grouping of Related Components: Grouping components that possess analogous functions or operate at the same frequency in tandem can assist in reducing EMI. For example, in a home theater amplifier FPC, the audio input and output components can be clustered together, and the power supply components for the amplifier can be grouped separately. This permits more efficacious shielding and filtering of each assemblage. By grouping related components, the shielding and filtering measures can be tailored more precisely to the specific EMI characteristics of each group.
C. Impedance Matching and Signal Integrity
Impedance Control: Maintaining a proper impedance match along the signal traces is elemental for signal integrity and to attenuate EMI. The impedance of the traces should be computed based on the idiosyncrasies of the signals being transmitted. For high-speed digital signals, the impedance is typically around 50 ohms or 100 ohms. Utilizing impedance-controlled FPC materials and adjusting the trace width, thickness, and dielectric constant can achieve the coveted impedance. Impedance matching ensures that the signal is transmitted without significant reflections, which can lead to signal distortion and EMI.
Signal Termination: Appropriate signal termination is requisite to preclude signal reflections, which can engender EMI. Termination resistors can be appended at the terminus of the signal lines to match the impedance and absorb the signal energy. For example, in a TV FPC that transmits video signals, termination resistors should be positioned at the receiving end of the differential pairs to ensure pristine signal reception and reduced EMI. Signal termination effectively dissipates the signal energy that would otherwise be reflected back along the trace, maintaining the integrity of the signal and minimizing EMI.
V. Conclusion
Mastering the EMC aspects in the design and production of FPCs for home appliances is a convoluted yet essential undertaking. By adhering to the guidelines presented in this article, manufacturers can augment the EMC performance of their products, ensuring reliable operation in the electromagnetic milieu of modern homes. Shenzhen Huaruixin Electronics Co., Ltd. is perpetually at the ready to dispense further succor and expertise in this regard, aiding home appliance manufacturers in realizing superior FPC designs replete with excellent EMC attributes.