Technical Insights into Customizing FPC Wireless Charging Coils and Modules
- Dec 05,2024
-
Share
The customization of FPC wireless charging coils for mobile phone induction fast charging transmitter and receiver module coils, along with FPC flexible circuit boards, involves multiple crucial aspects in the electronics industry:
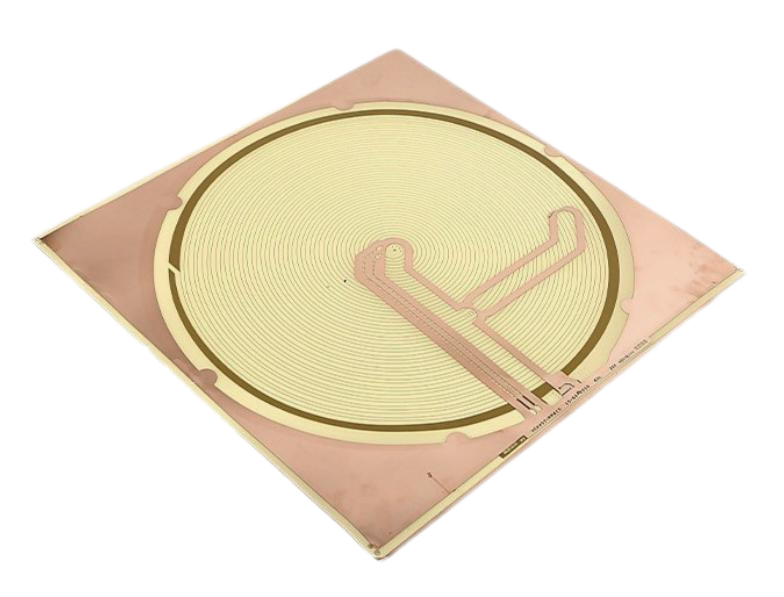
1. Precision in Electrical Parameters
Importance: Accuracy in electrical aspects like inductance, resistance, and Q factor is vital for coil performance.
Example: In a project, a specific inductance value of 5 μH at 100 kHz was required for optimal charging. Deviation of more than 0.1 μH from this value led to a significant drop in charging efficiency from 75% to below 50%. Resistance should be minimized to reduce power dissipation, and an ideal Q factor needs a balance of these parameters for efficient energy transfer.
Role of Coil Shape: The shape and structure impact magnetic field interaction. Circular coils offer magnetic field uniformity advantages (e.g., in a wireless charging pad, it had a more even magnetic field distribution compared to a rectangular design). Rectangular coils can be better for space-constrained applications like compact mobile phones.
Factors Affecting Magnetic Field: The number of turns, coil diameter, and inter-turn spacing influence the magnetic field's strength and distribution. Precise alignment between transmitter and receiver coils is crucial; a 2 mm misalignment in one setup caused a nearly 40% decrease in charging speed.
Dielectric Substrate: It should have excellent insulating properties and minimal signal attenuation.
Copper Considerations: Thickness and purity of copper matter. In a product development, switching from a 35 μm copper foil with higher resistance (causing excessive heat generation) to an 18 μm copper foil with higher purity improved performance by reducing resistance.
Adhesive and Coverlay: They need to provide flexibility and durability to protect the coil from mechanical stresses and environmental factors (e.g., a high-quality polyimide coverlay protects against scratches and moisture ingress).
Trace Design: Layout of conductive traces is complex. Minimizing parasitic capacitance and inductance is essential. Traces with smooth curves and appropriate widths reduce impedance. Redesigning narrow and sharp-angled traces to wider and smoother ones improved charging efficiency by about 20%.
Shielding and Grounding: Implementing ground planes and shielding vias minimizes crosstalk between adjacent traces to ensure reliable charging performance.
Heat Management: Heat generated during wireless charging due to resistive losses must be managed. Incorporating thermal dissipation mechanisms like thermally conductive adhesives or heat sinks (e.g., in a high-power module, a heat sink on the back of the FPC kept the coil temperature within a safe range; without it, temperature would exceed limits and cause performance degradation and potential damage).
Compatibility: Customized coils must be compliant with industry standards like Qi. In a case, a coil that passed internal tests but didn't work properly with some Qi-certified devices needed adjustments to achieve full compatibility for commercial integration.
Regulatory Requirements: Adhering to them ensures market acceptance and the safety and reliability of the end product.
Overall, in FPC wireless charging coil customization, attention to every detail is necessary, and collaborating with experienced partners can lead to innovative and high-performing wireless charging solutions to meet market demands.