As a proficient technical engineer engaged in the realm of FPC (Flexible Printed Circuit) manufacturing, the judicious selection of conductive materials serves as a linchpin for guaranteeing the optimal performance and unwavering reliability of FPCs.
Shenzhen Huaruixin Electronics Co., Ltd., renowned for its copious experience in FPC production and sales, is always enthusiastic about fostering in-depth discussions and knowledge dissemination with clients. In this blog, we will meticulously dissect the selection criteria and cardinal considerations pertaining to conductive materials in FPC design and production.
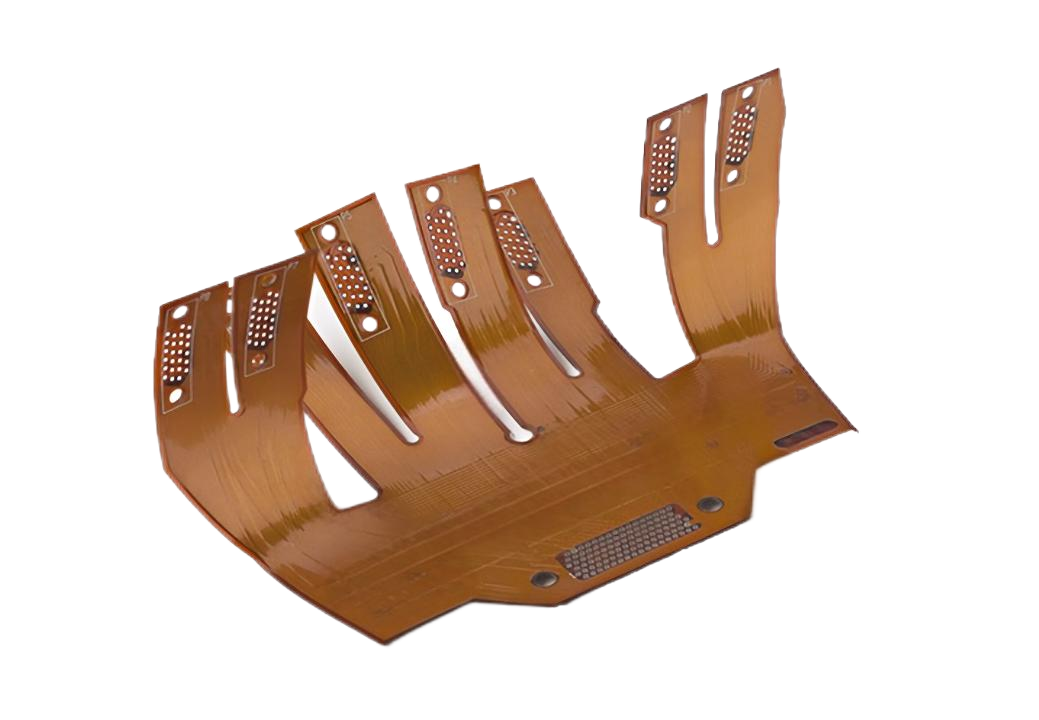
1. Types of Conductive Materials and Their Sophisticated Properties
A gamut of conductive materials find application in FPCs, each endowed with its idiosyncratic and intricate characteristics.
Copper, being the preeminent and ubiquitously employed conductive material, exhibits remarkable electrical conductivity. This property is of primordial significance for signal transmission, ensuring minimal attenuation and distortion. In high-speed digital circuits, for instance, copper conductors function as the conduit for expeditious and precise data transfer, owing to their ability to facilitate the seamless flow of electrical impulses. Copper also manifests relatively favorable ductility, endowing it with the capacity to endure a certain degree of mechanical deformation such as bending and flexing without succumbing to premature fracturing. However, copper is inherently susceptible to oxidation, especially when exposed to humid or corrosive milieus. To palliate this vulnerability, surface treatments such as electroplating with a thin yet precisely calibrated layer of nickel or gold are commonly implemented. The thickness of the plating layer demands meticulous control. A plating that is overly thin may prove inadequate in providing the requisite protection against oxidation and corrosion, whereas an excessively thick layer could engender escalated costs and potentially impinge upon the flexibility of the FPC.
Another material of note is silver paste. Silver, renowned for its superior electrical conductivity compared to copper, is often enlisted in applications where an extremely low resistance is non-negotiable, such as in certain power distribution circuits within FPCs. Silver paste can be deftly printed or coated onto the FPC substrate, thereby enabling the creation of exquisitely fine conductive patterns. Nevertheless, silver is a relatively costly material, and its long-term stability in specific environmental and operational conditions may raise concerns. Additionally, issues related to adhesion to the substrate can surface if the formulation is not optimized. The adhesion strength must be meticulously engineered to ensure a tenacious bond between the silver paste and the underlying substrate, lest delamination occur during the service life of the FPC.
2. Key Considerations in Conductive Material Selection: A Multifaceted Analysis
Electrical Conductivity Imperatives: The specific application niche of the FPC unequivocally dictates the requisite level of electrical conductivity. In RF (Radio Frequency) circuits, for example, a superlatively high conductivity is an absolute sine qua non to curtail signal loss to the barest minimum. In such scenarios, a synergistic combination of high-purity copper and meticulously engineered surface plating, such as a precisely calibrated thickness of gold plating, might emerge as the optimal solution. This plating not only augments the conductivity but also mitigates the oxidation propensity of copper. Conversely, for general-purpose low-power circuits, a standard copper foil with a defined thickness, which is determined through comprehensive electrical modeling and simulation, may adequately fulfill the conductivity requirements. The resistance of the conductive material must be accurately computed and measured using advanced metrology tools. For instance, by invoking Ohm's law and factoring in variables such as the length, cross-sectional area, and resistivity of the conductor, we can precisely prognosticate the expected resistance and make astute adjustments to the material and its geometric dimensions accordingly.
Flexibility and Durability: Pivotal for Longevity: Given that FPCs are routinely subjected to recurrent bending and mechanical stress, the conductive material must possess not only adequate flexibility but also robust durability. Copper conductors, in particular, need to possess a well-defined grain structure and an optimized thickness. The grain orientation and size can be manipulated through annealing and other metallurgical processes to enhance the material's ability to withstand flexing without cracking or fracturing. The adhesion between the conductive material and the substrate is of paramount importance. A feeble bond can precipitate delamination during flexing, culminating in open circuits and compromising the functionality of the FPC. Rigorous testing methodologies such as the flexural endurance test, which subjects the FPC to a predetermined number of bending cycles under controlled conditions, and the peel strength test, which quantifies the force required to detach the conductive material from the substrate, are indispensable for evaluating these properties. In wearable FPC applications, where extreme flexibility is the order of the day, special copper alloys or ultrathin copper foils, which are fabricated using state-of-the-art microfabrication techniques, may be contemplated to supercharge the flexibility while conserving satisfactory conductivity.
Cost Considerations: Striking a Balance: Cost invariably looms large as a decisive factor in material selection. Copper, in general, presents a more cost-effective alternative compared to silver. However, the overall cost equation encompasses not only the raw material cost but also the expenses associated with processing and any supplementary surface treatments. For mass-produced FPCs, even a minuscule differential in material cost per unit can snowball into a substantial impact on the total production cost. Therefore, a delicate equilibrium must be struck between performance and cost. In some consumer electronics applications, where cost containment is a preponderant constraint, a thinner copper foil, whose thickness is optimized through a comprehensive cost-benefit analysis, with streamlined processing parameters might be deployed to curtail costs without precipitously compromising performance. This optimization might involve leveraging advanced manufacturing technologies such as roll-to-roll processing and in-line quality control to enhance productivity and minimize waste.
Environmental Compatibility: Withstanding the Elements: The FPC is liable to be exposed to a diverse array of environmental conditions during its operational lifespan, encompassing temperature extremes, humidity fluctuations, and chemical substances. The conductive material should be endowed with the resilience to withstand these conditions without significant degradation. Copper, when fortified with appropriate plating, can exhibit a certain degree of resistance to oxidation and corrosion. In particularly harsh chemical environments, such as those encountered in industrial or automotive applications, special coatings or alternative conductive materials with enhanced chemical resistance may be essential. For example, in automotive FPCs that might be exposed to engine fluids and road salts, the selection of conductive material and its attendant protective measures need to be painstakingly devised. This could involve the use of corrosion-resistant alloys or the application of hermetic coatings to shield the conductive elements from the deleterious effects of the environment, thereby ensuring long-term reliability and functionality.
In conclusion, the selection of conductive materials in FPC design and production is a complex and multifaceted process that mandates a comprehensive and circumspect consideration of multiple factors. By meticulously appraising the properties of diverse conductive materials and adroitly matching them with the specific exigencies of the FPC application, we can engineer high-quality, reliable FPC products.
Shenzhen Huaruixin Electronics Co., Ltd. is wholeheartedly dedicated to proffering professional guidance and avant-garde solutions in this regard, and warmly welcomes continued communion and collaboration with clients.