In the ever-evolving landscape of electronics manufacturing, the bespoke creation of Flexible Printed Circuits (FPCs) – spanning thick copper soft boards, thick gold soft boards, hard gold soft boards, electrode sheet sensors, and adapter boards – emerges as a complex yet captivating domain. Shenzhen Huaruixin Electronics Co., Ltd., a vanguard in the FPC production and sales arena, has amassed a trove of knowledge and proficiency. Let's embark on a journey to unearth the pivotal elements that mandate astute consideration during this bespoke production odyssey.
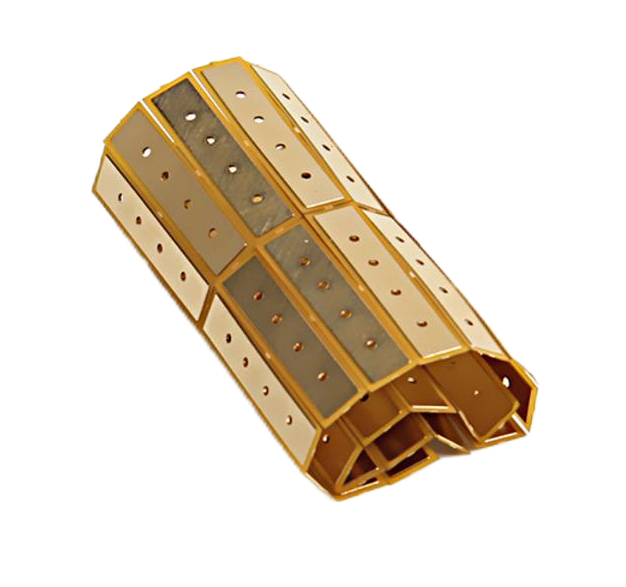
1. Material Selection and Compatibility: The Bedrock of Excellence
The inception of triumphant FPC production hinges on the sagacious choice of materials. For thick copper soft boards, the selection of copper foil with an apt thickness is non-negotiable. In applications clamoring for high current-carrying capacity, such as power modules in industrial paraphernalia, a thicker copper foil (ranging from 70μm to 200μm) takes center stage. However, thicker copper foils unfurl challenges in etching and flexibility. Our enterprise has instituted stringent quality control protocols to vouchsafe the uniformity of copper foil thickness. In a recent foray into a renewable energy inverter project, we sourced copper foil with a thickness tolerance of ±5μm. This exactitude in material selection empowered us to fabricate thick copper soft boards that could adroitly handle high currents sans excessive heat generation and with unfaltering mechanical integrity.
When it comes to thick gold and hard gold soft boards, the quality and thickness of the gold plating reign supreme. The gold layer not only endows excellent conductivity but also proffers corrosion resistance and sterling contact performance. In a project for a high-end consumer electronics device like a luxury smartphone, we applied a hard gold plating with a thickness of 0.2μm to the connectors. To ensure the adhesion and durability of the gold layer, we conducted exhaustive compatibility tests between the gold plating material and the underlying substrate. We also finessed the plating process parameters, including current density and plating time, to attain a uniform and flawless gold layer.
For electrode sheet sensors, the selection of sensing materials is a watershed moment. Diverse applications beckon different sensing materials. In a medical diagnostic device project, we harnessed a specific type of biosensor material that could detect minute traces of a particular biomarker. These sensing materials need to be artfully integrated with the FPC substrate. We have devised specialized techniques to ensure the proper adhesion and electrical connection between the sensing material and the FPC traces. Additionally, we pay scrupulous attention to the encapsulation of the sensing area to shield it from environmental vagaries while permitting efficient interaction with the target analyte.
2. Precision Fabrication Processes: The Artistry of Micro-Engineering
The fabrication of custom FPCs demands highly precise manufacturing processes that verge on the realm of artistry. In the case of thick copper etching, attaining the coveted pattern and thickness control is a Herculean task. We deploy advanced etching technologies, such as laser-assisted etching, which bequeaths more accurate control of the etching depth and pattern definition. In a project for a high-power LED lighting fixture, our precise etching process enabled us to create thick copper traces with a width tolerance of ±10μm. This level of precision ensured uniform current distribution and optimal heat dissipation, thereby enhancing the overall performance and lifespan of the lighting product.
Gold plating for thick gold and hard gold soft boards clamors for strict process control. We employ automated plating systems that can minutely regulate the plating parameters. In a production run for a high-frequency communication board, our plating process achieved a gold layer thickness uniformity of within ±0.02μm. This level of consistency is the linchpin for maintaining stable electrical contact and signal transmission in high-frequency applications.
For electrode sheet sensors, the printing or deposition of sensing materials onto the FPC necessitates specialized equipment and techniques. We utilize inkjet printing technology for its high precision and flexibility in depositing thin layers of sensing materials. In a project for an environmental monitoring sensor, we were able to print a sensing layer with a thickness of 8μm with peerless uniformity and repeatability. The curing process of the sensing material is also meticulously controlled to ensure its proper functionality and stability.
Adapter boards, on the other hand, require precise drilling and punching operations for component mounting. We enlist computer numerical control (CNC) machines with high positioning accuracy. In a project for a high-speed data processing unit, our CNC machines were able able to drill holes with a diameter tolerance of ±0.015mm, ensuring accurate component placement and reliable electrical connections.
3. Quality Inspection and Testing: The Sentinel of Reliability
A robust quality inspection and testing regime is the sentinel that safeguards the reliability of the custom FPCs. For thick copper soft boards, we conduct comprehensive electrical and mechanical tests. Electrical tests encompass resistance measurements and insulation resistance tests. In a project for a power distribution system, we measured the resistance of each copper trace and ensured that the insulation resistance was above a specified value (e.g., 100MΩ). Mechanical tests involve bend tests and tensile strength tests. The thick copper soft boards were subjected to repeated bending cycles (e.g., 10,000 times) to mimic real-world usage, and any signs of cracking or delamination were vigilantly monitored.
For gold-plated FPCs, contact resistance and adhesion tests are carried out. We use a four-point probe method to measure the contact resistance, and in a project for a consumer electronics device, we ensured that the contact resistance was within the acceptable range (e.g., less than 5mΩ). The adhesion of the gold layer was tested using a tape peel test, and any samples with poor adhesion were jettisoned and analyzed to ameliorate the plating process.
In the production of electrode sheet sensors, functionality and sensitivity tests are of paramount importance. We have cultivated custom test setups to appraise the performance of the sensors. In a project for a gas sensor, the sensors were tested for their response to different gas concentrations, and the sensitivity was calibrated to meet the application requirements. Any sensors that did not meet the specified sensitivity range were recalibrated or supplanted.
Adapter boards undergo signal integrity tests, including impedance measurements and time domain reflectometry (TDR) tests. In a high-speed data communication project, we ensured that the adapter boards had the correct impedance matching (within ±10% tolerance) and minimal signal reflection. Any boards that failed these tests were reworked or redesigned to optimize the signal transmission characteristics.
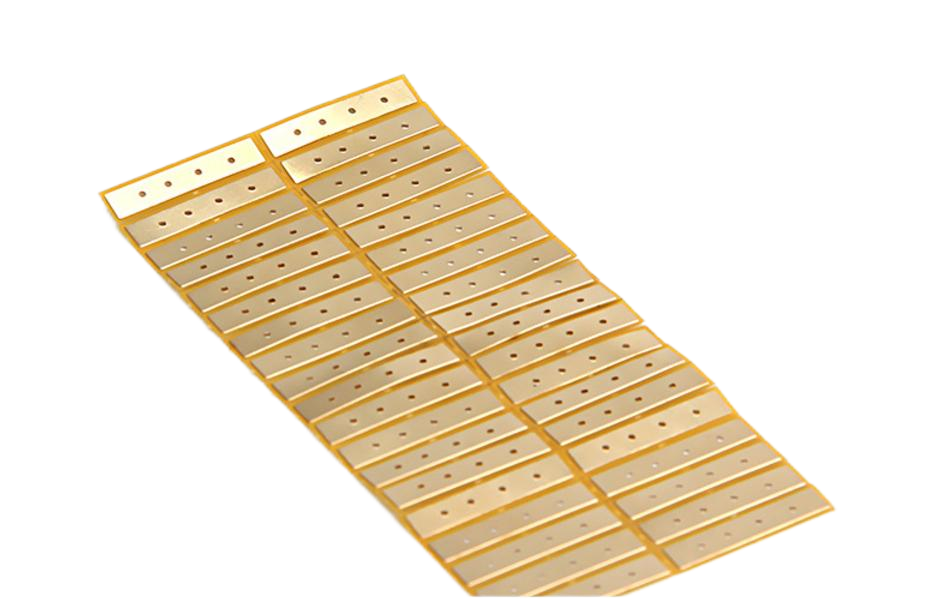
Shenzhen Huaruixin Electronics Co., Ltd. has a cornucopia of successful case studies. In a project for a hybrid vehicle, we produced a combination of thick copper and electrode sheet sensor FPCs. The thick copper FPCs were commandeered for power management in the vehicle's electrical system, and the electrode sheet sensors were integrated to monitor the battery health. Through our painstaking production process and quality control, the FPCs met the exacting requirements of the automotive industry, ensuring the reliable operation of the vehicle's critical systems.
Another success was in a project for a high-resolution display device. The FPC included hard gold plating for high-speed data transfer and a complex adapter board design. Our precise fabrication and comprehensive testing culminated in FPCs that furnished excellent signal integrity and mechanical stability, contributing to the superlative visual performance of the display device.
In conclusion, the custom production of FPCs such as thick copper soft boards, thick gold soft boards, hard gold soft boards, electrode sheet sensors, and adapter boards is a multifaceted tapestry of considerations. From material selection and fabrication processes to quality inspection and testing, each stitch requires the utmost finesse and acumen. S
henzhen Huaruixin Electronics Co., Ltd. stands poised to traverse these challenges and looks forward to collaborating with customers to transmute their innovative FPC-based projects into tangible realities.