In the realm of Flexible Printed Circuits (FPC), exposed vias are a vital component that requires painstaking attention during design and production. Shenzhen Huaruixin Electronics Co., Ltd., a top - tier professional in FPC production and sales, is here to offer in - depth insights on this matter.
What are Exposed Vias?
Exposed vias in FPCs are vias that are left uncovered and exposed on the surface, playing a crucial role in establishing electrical connections between different circuit layers and enabling signal transmission.
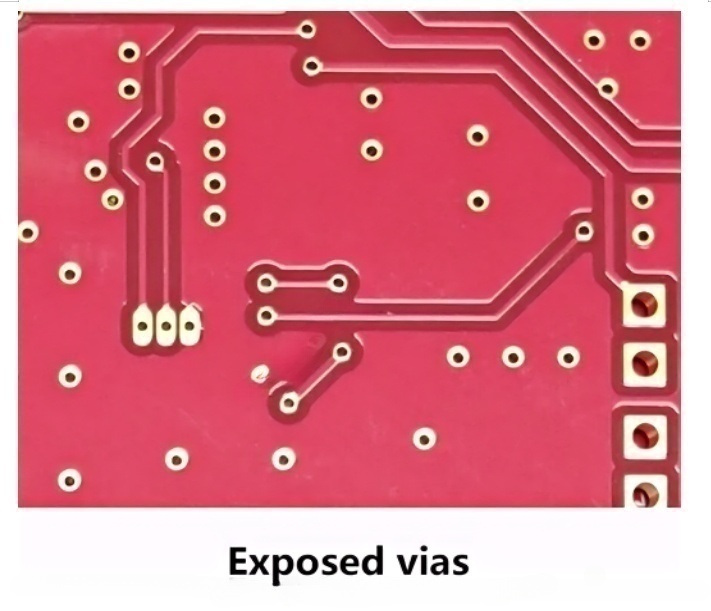
Design Considerations
1.Via Size and Density
The size of exposed vias must be carefully determined based on the FPC's electrical requirements. Smaller vias can increase circuit density but may complicate production and affect connection reliability. For high - speed signal transmission FPCs, 0.1mm - diameter vias might be used to reduce signal interference between layers, though this demands advanced manufacturing techniques. Vias density also matters. A high density in a small area can cause short - circuit issues during production or operation without proper design.
2.Location and RoutingThe location of exposed vias within the FPC layout is critical. They should be placed strategically to minimize the impact on signal integrity. When routing signals, avoid placing vias in areas that can cause signal reflections or crosstalk. In smartphone or handheld device FPCs, vias are usually kept away from the antenna area to prevent wireless signal interference. Also, the routing around vias should be smooth for stable signal flow.
3.Surface Finish and CompatibilityAs exposed vias are in contact with the environment, their surface finish is significant. A proper surface finish can improve solderability and protect against oxidation. Gold, nickel - gold, and organic solderability preservatives (OSP) are common finishes. The choice should match subsequent assembly processes and FPC materials. In high - humidity environments, a corrosion - resistant finish like gold is preferred.
Production Considerations
1.Drilling and Etching ProcessesDrilling and etching to create exposed vias must be highly precise. The drilling process should ensure the correct diameter and straight walls. Any deviation in drilling angle or diameter can cause problems later. Etching must be carefully controlled to remove unwanted copper cleanly. Advanced laser - drilling techniques are often used in modern FPC production for high - precision vias.
2.Cleaning and InspectionAfter creating vias, thorough cleaning is essential to remove debris and residues that can affect via performance. Visual inspection under high - magnification microscopes checks for defects like incomplete drilling, burrs, or damaged edges. Electrical testing methods, such as continuity and impedance measurement, ensure reliable electrical connections.
3.Process Control and OptimizationRigorous process control is necessary to ensure consistent quality in producing exposed vias. This involves monitoring and controlling temperature, humidity, and chemical concentrations during production. Process optimization should focus on reducing errors, improving efficiency, and minimizing the impact of vias on FPC performance. Optimizing drilling speed and feed rate, for example, can improve via quality and reduce production time.
Successful Design Cases
1.Smartphone FPC ProjectAt Shenzhen Huaruixin Electronics, we designed an FPC with exposed vias for a smartphone's high - speed data transmission and power distribution. The 0.15mm - diameter vias balanced density and manufacturability. Their locations were optimized to avoid antenna and sensitive - component interference. A gold surface finish provided excellent solderability and corrosion resistance. Advanced laser - drilling and precise etching techniques were used in production, resulting in high - performance data transmission with minimal signal loss and great smartphone functionality.
2.Automotive Electronics FPC
For an automotive electronics FPC, we designed exposed vias for sensor signals and power connections. The vias had a slightly larger diameter for reliable connections in the harsh automotive environment. The layout prevented crosstalk. A nickel - gold surface finish was chosen for durability. The production process had strict quality control with multiple cleaning and inspection steps, and the FPC has been working successfully in automotive systems, showing the strength of our design and production methods.
In conclusion, designing and producing exposed vias in FPCs involves many complex considerations. At Shenzhen Huaruixin Electronics Co., Ltd., we have the expertise and experience to handle these challenges. We welcome new and old friends to communicate and exchange ideas as we pursue excellence in FPC design and production for various applications.