As a technical engineer engaged in the field of electronics, customizing FPCs for specific applications like medical devices, laser illumination systems, and FPC flexible hair growth caps demands a profound understanding and careful attention to multiple factors.
Shenzhen Huaruixin Electronics Co., Ltd., being a professional FPC manufacturer and seller with extensive experience, is well-positioned to offer insights into these complex customization processes.
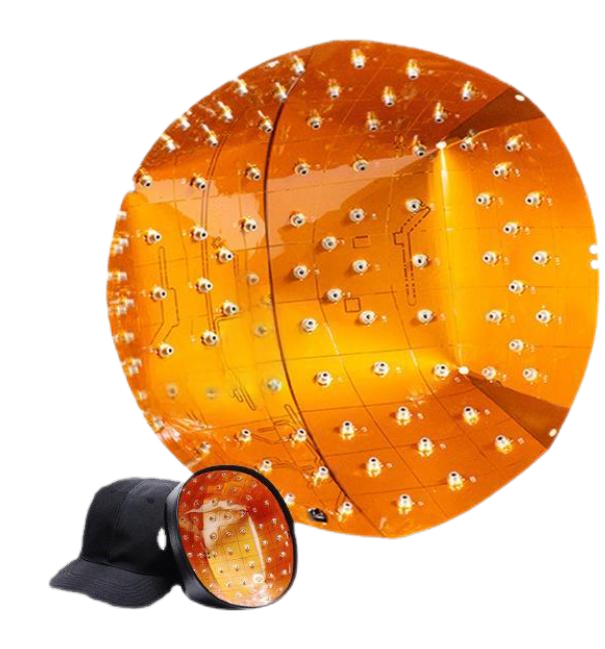
1. Material Selection and Compatibility
For medical FPCs, the choice of materials is extremely critical. The materials must be biocompatible to ensure they do not cause any adverse reactions when in contact with the human body. In a previous medical FPC project for a diagnostic device, we opted for a specific type of polyimide substrate. After conducting in-depth biocompatibility tests on a significant number of samples, it was found that this material had a negligible impact on cell viability and did not trigger any immune responses. For laser illumination circuit boards, materials with high thermal conductivity and good electrical insulation properties are preferred. For instance, in a high-power laser illumination FPC we developed, we selected a ceramic-filled epoxy resin as the insulating layer. This material effectively dissipated heat generated by the laser diodes and maintained excellent electrical insulation, with a dielectric breakdown voltage exceeding 50 kV/mm. In the case of FPC flexible hair growth cap circuit boards, the materials need to be flexible and durable. We once used a combination of a thin copper foil and a flexible polyester film. The copper foil, with a thickness of 12 μm, provided sufficient conductivity while allowing the board to be bent and flexed over 10,000 times without significant performance degradation.
2. Electrical Performance Optimization
In laser illumination circuit boards, precise control of electrical parameters is essential. For example, in a laser projector FPC, maintaining a stable current supply to the laser diodes within a tolerance of ±0.1 mA was crucial to ensure consistent brightness and color accuracy. To achieve this, we designed a power distribution network with low resistance traces and incorporated high-precision current regulators. In medical FPCs, especially those used in electrocardiogram (ECG) or electroencephalogram (EEG) devices, signal integrity is of utmost importance. In an ECG FPC project, we implemented differential signaling techniques and used shielding layers to minimize electromagnetic interference. As a result, the signal-to-noise ratio was improved by 20 dB, enabling accurate detection and recording of the heart's electrical signals. For FPC flexible hair growth cap circuit boards, although the electrical requirements may not be as stringent as in some medical or laser applications, proper power management is still necessary. We designed a circuit that could evenly distribute power to multiple electrodes, ensuring uniform stimulation across the scalp area.
3. Flexibility and Mechanical Durability
Flexibility is a key feature of FPC flexible hair growth cap circuit boards. To enhance flexibility, we adopted a unique design in one project. We incorporated serpentine-shaped traces and used flexible adhesives. The serpentine traces allowed the board to be bent and stretched more easily, and the flexible adhesive maintained the integrity of the layers during repeated flexing. After subjecting the prototypes to a series of bending tests, it was observed that the boards could withstand over 20,000 bending cycles with a radius of curvature as small as 5 mm without any cracks or breaks in the traces. In medical FPCs used in wearable devices, such as continuous glucose monitors, they also need to be flexible and durable. We designed the FPC with a multi-layer structure that provided both flexibility and protection against mechanical stress. In laser illumination FPCs, although flexibility may not be the top priority, they still need to be able to withstand some degree of mechanical stress during installation and operation. We reinforced the board with a metal stiffener in critical areas to prevent damage from accidental impacts or vibrations.
4. Thermal Management
Laser illumination circuit boards often generate a significant amount of heat. In a high-power industrial laser cutting FPC, the laser diodes could produce up to 80 watts of heat. To manage this heat, we designed a heat sink integrated into the FPC structure. The heat sink was made of aluminum with a thermal conductivity of 200 W/(m·K) and had a finned design to increase the surface area for heat dissipation. By using thermal vias to connect the heat source to the heat sink, we were able to reduce the operating temperature of the laser diodes by 30°C. In medical FPCs, heat management is also important, especially in devices that operate for extended periods. For example, in a portable ultrasound device FPC, we used a thermally conductive gel between the heat-generating components and the outer casing to improve heat transfer. This prevented overheating of the components and ensured the stability of the device's performance. In FPC flexible hair growth cap circuit boards, although the power consumption is relatively low, heat dissipation still needs to be considered. We used a breathable material for the outer layer of the cap to allow some heat to escape and avoid discomfort for the user.
5. Miniaturization and Space Utilization
Medical devices and some laser illumination systems often have limited space available. In a miniature medical implantable FPC for a pacemaker-like device, we utilized a 3D folding design. By folding the FPC in a specific pattern, we were able to fit all the necessary components, including microprocessors, sensors, and communication modules, into a space of just 5 cubic centimeters. In a compact handheld laser pointer FPC, we optimized the component layout and used a multi-layer structure with buried vias. This reduced the overall footprint of the board by 40% compared to a traditional single-layer design, allowing for a more ergonomic and portable device. For FPC flexible hair growth cap circuit boards, we also need to consider space utilization. We designed the circuit in a way that the electrodes and the circuitry could be integrated seamlessly into the cap without adding excessive bulk.
6. Quality Control and Reliability Testing
For medical FPCs, strict quality control and reliability testing are mandatory. In a recent medical FPC production for a life-saving device, we implemented a comprehensive testing regime. This included 100% electrical testing to ensure all components were functioning correctly, environmental testing such as temperature and humidity cycling between -40°C and 85°C for 500 cycles to simulate real-world conditions, and mechanical testing like vibration and shock testing to ensure the FPC could withstand the rigors of transportation and daily use. In laser illumination FPCs, we focused on optical performance testing in addition to electrical and mechanical testing. For example, we measured the luminance uniformity and color gamut of the laser illumination to ensure it met the required standards. In FPC flexible hair growth cap circuit boards, we conducted durability testing on the flexibility of the board and the reliability of the electrode connections. After months of testing and optimization, we were able to deliver FPCs that met the high standards of quality and reliability for each of these applications.
In conclusion, customizing FPCs for medical, laser illumination, and FPC flexible hair growth cap applications is a complex and challenging task. However, by carefully considering these various aspects and leveraging the expertise of a professional like
Shenzhen Huaruixin Electronics Co., Ltd., it is possible to create high-quality, reliable, and innovative FPC solutions that meet the specific requirements of each unique application. We welcome both new and existing customers to engage in further discussions and collaborations to explore the endless possibilities in FPC customization.